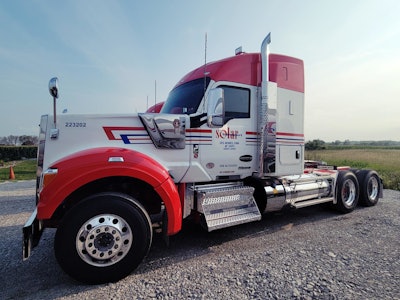
CCJ Innovators profiles carriers and fleets that have found innovative ways to overcome trucking’s challenges. If you know a carrier that has displayed innovation, contact CCJ Chief Editor Jason Cannon at [email protected] or 800-633-5953.
The transportation industry saw record-breaking fuel prices in 2022, and with diesel prices average in excess of $4 a gallon in the U.S., mistakes are quite costly.
Des Moines, Iowa-based fuel hauler Solar Transport, which has about 220 drivers and 120 trucks serving the Midwest and Rocky Mountain regions, was on track to hit almost $2 million in fuel delivery errors in 2022, said Director of Driver Services Jason Jones.
Industry studies regarding tank-truck usage patterns across the U.S. show that the unintended mixing of octane types at a fueling site happens once in every 14,000 deliveries nationally. A diesel/gasoline mixup occurs once in every 45,000 fuel drops across the country, according to information compiled in a 2021 Civacon case study of R.B. Stewart Petroleum Products Inc.’s use of the CivaCommand Smart Tank System.
Solar Transport made 126,713 deliveries in 2022. With so many manual steps drivers perform when dropping fuel, Jones said cross-drops – when the wrong product is loaded into a tank – are bound to happen.
While Solar Transport continues to seek ways to further reduce errors, it has seen a 52% decrease in cross-drops and a drop in turnover from 56% to 23% since implementing customized automated workflows.
“The driver’s job is very manual in terms of when he gets to the location. He has to hook up all the hoses to the appropriate compartment, make sure that he loads it correctly and so forth. There are a lot of steps that take place for delivery,” Jones said. “We had an overabundance of missed pulls (when a fuel hauler pulls the wrong product or the wrong supplier for the customer directive), which led to cross-drops, which turns into huge expenses on our behalf. That's where we wanted to come back and adjust our workflow with how the driver proceeds with the order… We've saved thousands, if not millions, of dollars by creating an automated workflow.”
The carrier worked with Motorcity Systems to customize a workflow to reduce cross-drops and the resulting costs. Based on Solar Transport’s specific needs, Motorcity connected the dots using its cloud-based TORQUE integration platform and real-time driver communications and visibility app, RELAY, to improve operational efficiency and the driver experience.
Solar Transport has integrated operational data and workflows between its Transportation Management System (TMS), ELD telematics, workflow and RELAY dispatch-driver messaging application using TORQUE.
Solar Transport’s driver hours-of-service duty status and vehicle telematics data from Samsara is integrated with its dispatch-driver messaging platform. The integration gives dispatchers better visibility of mission-critical operational, safety and compliance information.
Solar Transport’s workflow – further tailored based on driver input – is deployed on every driver tablet via a custom Solar Mobile app developed by Eleos.
“Our customized workflow is different from anybody else out there,” Jones said. “The biggest thing I want to point out is when we choose vendors and try to create workflows and understand how they work, we like to involve our drivers, and they're able to help us out because … they're the ones that are doing it day in and day out. I think it has paid huge dividends to be able to include these drivers in our discussions and in our game plan.”
A driver recommendation that was included in the app is a step Solar Transport never had before. That recommendation was to have a step where the driver reports back to dispatch what product was loaded so it could be confirmed that’s what was ordered prior to the driver taking it out for delivery. Jones said that step has prevented loading errors that previously weren’t being caught until the driver had already dropped the wrong product into the tank at the convenience store.
Once that error has been made, the process to undo it is extensive and costly.
If a cross-drop occurs, it shuts down pumps at the store, and the store isn’t able to sell product until the error is corrected. The driver then has to take the time they would spend making another delivery pumping 20,000 gallons of now-contaminated product back into the trailer and hauling it 300-plus miles away to be recycled, also taking that equipment out of service. The product then has to be replaced at the store.
“By us creating this workflow, it puts a driver in a better position and provides the checks and balances necessary to really avoid the huge errors of the $80,000 to $100,000 errors that we've experienced in the past,” Jones said.
With the automated workflow, a driver can login to their tablet the night before or day of their shift to view what loads have been assigned to them. Jones said some drivers haul one load a day, and some do six or seven. With the app, drivers can see their pickup and drop-off locations, what products they will be hauling, site maps of the stores (where to pull in, where the tanks are, location of any potential hazards and the best exit route) they’re dropping at and inventories, any special instructions on the order and more.
When a driver starts their day, they select their first load in the workflow, and it’s communicated back to dispatch that they’ve begun their trip and are headed to the terminal to load. Arrival and departure times at both the loading point and dropping point are captured, and that data is provided to the office. At the terminal, or loading point, the driver validates in the workflow that they have picked up the product and which product they loaded before heading to the dropping point, or convenience store.
At the store, they follow the workflow: stick-measure the tank to confirm the inventory and that it will fit, and validate color-coded tags on the tanks to ensure they’re dropping in the proper area. Once the drop is complete, they fill out a form in the app that includes details like confirming they stuck the tank, if they had a wait time or whether they had to move the truck to access another drop.
When that process is complete, the automated workflow triggers the next load, and they repeat the same steps. Drivers aren’t able to work on another load until the previous one is finished.
The biggest benefit to the workflow, Jones said, is the real-time updates to load changes. Motorcity connects with Solar Transport’s TMS and notifies the driver of any changes the moment they’re made.
“There's a constant sync of letting the driver know if there was any changes made to a particular order, where before we could change something and drivers wouldn't know about it,” he said. “All of a sudden, they've delivered to the wrong location or delivered the wrong product because they didn't have the update.”
Similarly, the customer also receives real-time updates.
Jones said when drivers feed information into the dispatch system, it sends that “extremely valuable” information – like product and supplier details – amount of gallons being delivered, estimated times of arrival and more, to the customer.
And the customer and driver satisfaction has proven the app beneficial in a short period of time.
“If we're able to create capacity with our customers and have the trucks and drivers available, that gives us the flexibility and capacity to bring on new customers, which we've been able to add,” Jones said.
And he said driver feedback has been phenomenal. Drivers have reported that the workflow has made it easier to train new drivers, easier to deliver to new locations with the site maps, and easier to determine if loads are going to fit with clear visibility into inventories in the ground at certain locations.
He said Solar Transport wants to see a greater percent decrease in cross-drops and is making additional investments in technology to do that and improve customer and driver satisfaction.
The carrier also began using an imaging app through EBE Technologies that allows drivers to scan their paperwork from inside their truck, which then is entered into the automated workflow system that shares that information with the customer and back office electronically. Jones said the carrier is now working to onboard an optical character recognition solution, also through EBE, to read that paperwork and enter the bill of lading information on behalf of the driver to reduce errors.
“We're going to continue to push, providing these drivers with the resources and the tools necessary to do their job,” he said.
The CCJ Innovators program is brought to you by Bendix, Comdata, Freightliner Trucks, SkyBitz and Valvoline.