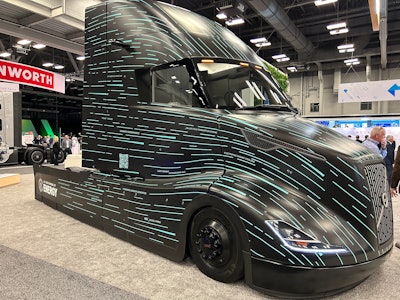
Volvo's SuperTruck 2, the fruits of a public-private partnership with the U.S. Department of Energy (DOE), was challenged to achieve a 100% freight efficiency improvement over its submitted 2009 baseline. And there were (ironically) engineering headwinds.
SuperTruck is mostly a concept and engineering exercise, so parts procurement can be a challenge, and in some cases they must be custom-made. That can be a tough hill to climb in the best of times, but Volvo faced them while the supply chain was unraveling during a pandemic.
Volvo Trucks, however, not only achieved the DOE objective but also exceeded expectations with a 134% increase in freight efficiency.
Volvo's SuperTruck 2 made its first public appearance last month at the American Trucking Associations’ 2023 Management Conference & Exhibition in Austin, Texas, and while it is very much a concept vehicle – or as Volvo Trucks North America President Peter Voorhoeve calls it, "an innovation lab" – it's also a viable test bed for technologies the company could one day roll out on the highway.
"We can try out things," Voorhoeve said, "and discover the things that we should and should not do."
Among the biggest learnings from SuperTruck 2 was something the company has known for many years: friction is bad. However, what became apparent in the quest for improvement is that a conventional driveline is as close to optimized as it's going to get. If Volvo wanted big gains, the truck has to have a fluidity to it movement.
"One of the things that we learned is, in order to come to a higher performance, it’s not on the driveline you need to work with," Voorhoeve said. "It’s aerodynamics."
The aggressive hood slip of Volvo's second Super Truck leads to a panoramic view from the driver's seat. You can't even see the hood while seated.
Starting with a cab perfectly wedge-shaped from front to back including a raked and custom-made wraparound windshield, the front end is designed around a downsized cooling package, a fully aerodynamic trailer with gap fairings, skirts and boat tail, and includes air-actuated adjustable ride height. Volvo Trucks also replaced the traditional hood and cab mounted mirrors with a streamlined camera monitoring system to reduce drag by more than 4%.
The entire tractor trailer combination was designed to smoothly displace air with minimal resistance, resulting in 50% lower drag than Volvo Trucks’ 2009 baseline – a roughly 20% improvement in aerodynamic drag over Volvo Trucks’ SuperTruck 1. Around two-thirds of the drag reduction in SuperTruck 1 over the 2009 baseline came from trailer aerodynamic treatments: optimizing the skirt and boat tail. Since SuperTruck 2 also boasts optimized trailer skirts and boat tail, most of its aerodynamic gains over SuperTruck 1 can be attributed to a brand-new cab design, including a radically different windshield, while SuperTruck 1 was a slightly modified version of a VNL 670 cab. SuperTruck 2 demonstrated the potential for significant aerodynamic gains from changing the Body-in-White, Voorhoeve said.
DOE’s SuperTruck 2 program promotes research and development to improve the freight- efficiency of heavy-duty Class 8 long-haul tractor-trailer trucks. The program aims to accelerate the development of cost-effective advanced efficiency technologies not currently available in the market. For SuperTruck 2, all participating OEMs were given the goal of demonstrating more than 100% improvement in vehicle freight efficiency [ton-mile-per-gallon]. Volvo Trucks met that goal and exceeded its internal stretch goal of 120% freight efficiency improvement relative to the 2009 baseline, achieving 134% under real world demonstrator validation.
In addition to the aerodynamics advancements, engineers implemented several weight reduction strategies to achieve a significantly reduced curb weight of 27,000 lbs. for the combined truck and the trailer. VolvoTrucks chose a 4x2 configuration, which is not common in the U.S., but is frequently utilized in Europe using fewer axles for the same payload. The truck was designed so it could be applied to a 6x2 or 6x4 configuration, but that was not part of the specific demonstrator validation for this program. The shorter cab design is lightweight and paired with an aluminum chassis that uses a lightweight optimized drive axle system with a single composite driveshaft.
Volvo Trucks worked with the project partner trailer manufacturer Wabash National to incorporate a custom, lightweight aerodynamic trailer with an optimized aerodynamic shape of the full truck and trailer to appear as one seamless unit, and worked with Michelin on an experimental, new, lighter rubber compound with a lower rolling resistance and used a smaller 19.5-inch tire on both the SuperTruck 2 and its custom trailer.
The shape of the truck and learnings from aerodynamics and light-weighting are the two things most likely to be seen on mass production models sooner rather than later, Voorhoeve said.
Voorhoeve noted that the project team deliberately focused on driving in real world conditions for testing, emphasizing that data wasn’t just gathered in a lab or on flat, empty roads with optimal conditions and a light load. "Instead, our SuperTruck 2 was tested in real-world scenarios on roads with traffic and elevation changes with a GCVW of 65,000 pounds,” he said. “This is the most aerodynamic and efficient truck Volvo has built to date, and we achieved a freight efficiency that demonstrates the potential for technology innovations to be developed commercially. Our engineers have already begun implementing some of the learnings from SuperTruck 2 into our future truck models. The future of trucks is just around the corner.”
Volvo Trucks' SuperTruck 2 also features a 48-volt micro hybrid system that acts as a generator with an integrated starter. This provides power for driver comfort features, including an all-electric HVAC system that allows the driver to avoid idling during rest breaks and still have power for amenities.
SuperTruck 3
Volvo's focus on aerodynamics will come in handy as it turns it attention to SuperTruck 3, as that truck won't include a diesel powertrain at all.
"Aerodynamics is always important, but especially so as we move from miles per gallon to miles per killowat hour," he said. "The lower the resistance, the better the efficiency. Aerodynamics always leads to better energy efficiency."
Voorhoeve said SuperTruck 3 will be battery electric with a targeted 400 mile range, but it will be focused on regional applications. The third generation super tractor project will also include the development of a megawatt charger.
Among the learnings from the first and second generation Voorhoeve expects to filter into the third generation are the company's heavy use of light-weighting and a single axle 4x2 configuration, among other elements, like the use of carbon fiber.