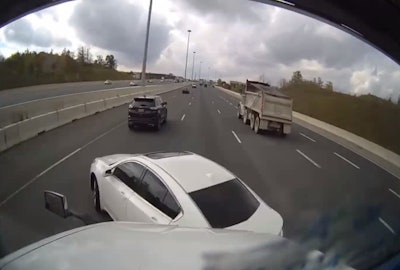
A carrier was able to exonerate one of its drivers in an accident that occurred just two weeks after that truck received a video monitoring system installation. A driver-facing dash camera showed that the driver was not distracted or tired; the telematics systems proved the driver wasn’t speeding; and the ELD verified the driver was within their hours of service limits. A forward-facing dash camera showed that the passenger vehicle involved had cut the driver off and hit the front of the truck.
This was an illustration in a recent report Effective Strategies to Improve Safety by the National Surface Transportation Safety Center for Excellence that involved nine carrier case studies. The study shows carriers that implemented video monitoring saw a 53% to 66% reduction in accidents. In the study, eight of the nine carriers used technology – like dash cameras and automatic emergency braking and lane-departure systems – to improve safety.
A recent webinar hosted by GPS Insight highlighted this study and determined five can’t-skip ingredients for an effective fleet safety recipe. Technology is No. 4 on the list, followed by training. The top ingredient is buy-in, followed by consistency and being proactive.
“There are just so many fleets – not just in the United States but across the world – that are always looking for ways to improve safety,” said Matthew Camden, senior researcher with the Virginia Technology Transportation Institute. “But a lot of times we hear that fleets don't necessarily know where to turn and what they should try.”
The study identified strategies among the nine fleets that were successful – and some even unsuccessful – in reducing crashes and improving safety performance. Camden said some faced barriers from coming up with a plan and obtaining equipment to understanding what problems needed solving and how to evaluate that.
While the implementation of safety measures is going to depend on a per-feet basis, Rick Harland, assistant director of fleet mobility services for the city of Austin, Texas and former fleet manager at Time Warner, offered several strategies: develop data-driven policies; implement a safety culture from leadership down; use auditable technology; and set key performance indicators to establish a method for continuous improvement.
Here's what the experts had to say per ingredient:
Buy-in
It starts with leadership, Camden said.
“Some of the carriers that participated in this study did try some strategies that weren't very successful … I really honestly think that the strategies that these companies tried, and they weren't a great fit for their organization, came down to how those programs were rolled out, implemented and supported by the leadership in the company,” he said. “So I think that it just really gets at the importance of having that culture and the people there to support the ongoing success and evaluation of safety programs.”
In a flash poll within the webinar that asked “have you had trouble getting drivers or other stakeholders in your company or organization to buy into safety,” the overwhelming response was yes.
In a separate webinar – this one hosted by the Truckload Carriers Association – that addressed how carriers can move from talking about safety to actually operationalizing it, Alicia Echols, director of safety and compliance at Bennett Heavy and Specialized, agreed that leadership is responsible for creating a strong safety culture.
She said one of the most successful strategies her company is doing to achieve that, in addition to a quarterly safety meeting, is a driver all-call held on the third Friday of each month where the company shares performance metrics and recognizes positive safety behavior and delivers incentives. It also includes talks about safety trends and how to improve in certain areas. Sometimes guests join; for example, one of the company’s recent all-calls included a representative from the Georgia Department of Public Safety who talked about the CVSA Road Blitz.
“What we found is that when we have that type of communication and collaboration, we're better equipped to identify gaps and communicate risks,” Echols said, advising carriers to blur the line between safety and operations by facilitating a deeper connection; don’t isolate them.
Wayne Transports also addresses the safety culture from the top down with weekly in-house safety videos that involve leadership and other members of management.
Paul Schmitz, director of safety at Wayne Transports, who also joined the TCA webinar, said the three- to five-minute videos are sent out every Monday to all employees, not just drivers.
“Communication in this industry has always been challenging,” he said. “Drivers and others in the company, they come to expect safety from safety professionals; they hear from us all the time. When you get leadership saying and showing examples of safety expectations, that's when the culture changes. We push to get as much involvement from every level … but the leadership is key to making sure that message is not lost.”
Consistency
The rules must apply to everyone with no exceptions.
Camden said because it’s hard right now to find drivers to fill seats, some carriers have compromised on their hiring criteria.
“A couple of the companies who participated in this study, they made exceptions to (their hiring practices), and those drivers were involved in collisions,” he said. “That is a recipe for disaster from a liability standpoint and your safety performance.”
He said those carriers saw major improvements in their safety performance when they stopped making those exceptions.
Echols said Bennett sets very clear safety goals and expectations for its drivers from the beginning, and the carrier regularly tracks and communicates progress on those goals.
Without excellent safety statistics to back up its drivers’ performance, the company couldn’t haul the materials it does, which includes ammunition, explosives and other Hazmat materials.
And she said the No. 1 cause for a safety program to fail or not to be as effective is lack of communication.
“I think that if you miss the mark on communicating out your why, then you're going to have people that don't really understand what you're trying to do,” Echols said. “We encourage open communication between drivers and management. I've had conversations with our drivers that have resulted in policy changes. We never want to isolate our drivers or make them feel like they aren't part of the team because they're the eyes and ears on the road.”
Alex Furl of GPS Insight said he has seen situations where a driver addresses a safety concern and is dismissed by management, so it’s important to increase transparency between drivers and supervisors, especially when it comes to safety data.
Schmitz said if drivers don’t have that data, they can’t understand what’s going on and how to fix what’s broken.
Using technology to be proactive
Reaction means something bad has already happened.
“For an active safety culture, it takes passion; it takes focus; and then, most of all, it takes action,” Schmitz said. “It takes action, not reaction. And so many fleets are reactive. In today's world of trucking, if you're not using … technology to assess the risk and manage the risk of your fleet, you're basically reactive.”
In another flash poll posted in the GPS Insight webinar, 82% of attendees who responded said they do use safety technology, and the majority said they would most like to add automatic emergency braking (AEB) systems. In the NSTSCE study, carriers that used AEB systems saw a 56% reduction in rear-end accidents.
There’s AEB, telematics, lane-departure and blind-spot warnings, dash cameras with real-time alerts and driver coaching and so much more. How does a carrier choose a vendor with so many options on the market?
Schmitz said it’s about identifying what problems your company needs to address and then peeling back the layers on each vendor to determine what best suits those needs.
He suggests asking other safety professionals what they’re using, how long they’ve had it, does it work and is support readily available. He also said it’s important to go beyond sales and meet with vendors’ development teams to understand their vision for the future of the product and learn how they will maintain their relationship with you. His advice to tech vendors is to seek out transportation companies to serve as advisors for their products. Wayne serves in an advisory role for Idelic.
Echols said a great way to determine if your company can have a long-term relationship with a vendor is if that tech partner listens to your recommendations and actually takes action on them.
Training
Continuous training is the fifth can’t-skip ingredient, whether it’s online, in the classroom, on the road, video-based coaching or automated coaching alerts.
“These vehicle-based technologies produce so much data on individual driver trends and driver safety; that's a wealth of information that companies can use to train their drivers on the specific risks that particular driver has,” Camden said.