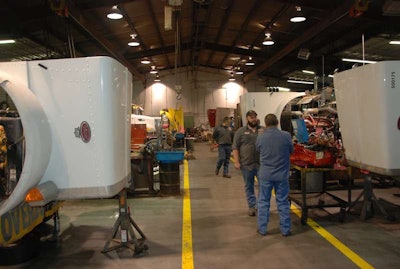
This is the third of a multi-part series on how drivers and the maintenance department work together to increase uptime. The first installment, “Pre-trip training, follow up critical in uptime goals” can be found here. The second, “Supporting drivers by addressing issues, incentivizing inspections” can be found here.
Keeping a commercial truck running requires a multi-pronged approach that often involves communication between people – drivers and technicians – that could be hundreds of miles apart.
A generation ago, drivers wrote down their maintenance needs and passed a copy on to the shop floor. That’s still a practice employed today but it’s largely been replaced by electronic communication.
Little Rock, Ark.-based Maverick Transportation uses a Qualcomm system to help coordinate the correspondence between the driver and repair shop, which includes information about the issue at hand and what time the driver wants to bring the truck in for service.
“The maintenance coordinator will take it and go into our scheduling board, which we have for each shop location, and they’ll find an open bay and schedule that equipment in that bay as close to that time frame as they can,” says Maverick’s Director of Maintenance Brent Hilton.
Once the truck arrives, the driver checks in with the shift supervisor who ushers the truck in for service.
“At that time, it’s on us to make sure we’re pulling our weight and getting them in and out on those times we told them we would,” Hilton says.
In events when additional repairs are needed, Maverick uploads a change in plans into its driver portal, which pushes an updated status notification directly to the driver’s cell phone.
Fleets that manage their own maintenance have the flexibility to move pieces around as they see fit. Leased operations have to factor in the actual service provider, but PacLease Maintenance Manager Rick Tapp says that doesn’t mean the service is any less personal. In fact, it doesn’t even have to be sophisticated. Tapp says most of his service shops have drivers’ cell phone numbers readily on hand.
“We can text drivers or call drivers while they’re on the road and say ‘hey, we’ve got the part in that we had ordered for your truck’ or ‘you’re coming due for service’ or ‘hey, we need to do this on your truck because we’ve been notified there’s a campaign on it. When’s your next day off?’”
Personal communication is key
Transervice’s Vice President of Maintenance Taki Darakos says not all communication can be – or should be – handled electronically. He suggests clearly spelling out the expectations of maintenance, and the communication flow between the driver and technician, as part of the on-boarding process.
“We try to have regular participation with driver meetings with ‘this is how the vehicle condition reporting is going to work. Here’s your contacts in the shop and here’s the flow,’” he says. “I always relay it back to a symphony or a band. Everything’s got to be in synch and going off at the appropriate time so it all sounds good. If the drivers aren’t doing their piece or the shop isn’t doing their piece, it becomes a problem.”
Jem Blair, vice president of safety for Alabama-based WTI Transport, says making a game of maintenance among the drivers can have an impact without involving the service bay.
“Drivers are a very competitive and if you take them out as a group and have them pre-trip commercial vehicles they are quick to point out to their peers what they missed,” says Blair, a 30 year veteran of the industry. “It’s actually kind of fun.”
To get the highest level of accountability across the board, Darakos says actively participating in drivers meetings can provide helpful feedback.
“My guys hate it when I go into a [driver] meeting and say, ‘is the shop taking care of you’ because it is kind of opening Pandora’s box,” he says. “But to some extent, I think when there’s a little bit of smoke there is fire there.”
“If we start to see an issue with guys not checking their tires on pre-trips, we’ll say ‘hey, can we come to your next driver meeting,” Tapp adds. “We want to review this topic with your guys.”
Keeping a truck running, Darakos says, can be a self-fulfilling prophecy in that drivers who are happy with their equipment tend to take better care of it.
“This is a rolling office. [Drivers] are in it more time than they are with friends and family. It may not be a pressing need for that button to work … but we have to get to it and it can’t be put off forever,” he says. “You would want everything to work in your house or your car and we need to take that same approach with the driver. A happy driver is someone who is going to be more engaged and they’re going to take better care of that piece of equipment.”