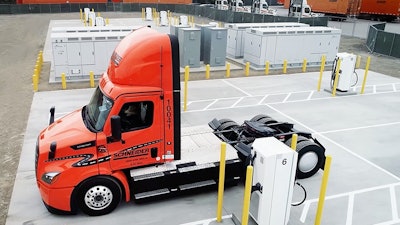
Capitalism fuels innovation. In 2016 W. Michael Cox and Richard Alm described that in the economic system known as capitalism, “markets mobilize the incredible power of human ingenuity, encouraging individuals and companies to discover better ways to achieve greater abundance by increasing supply and lowering costs.” Capitalism is one of those banner terms that rally groups to be advocates or cynics. It is a foundation of how ideas go from concept to market adoption.
The Wright Brothers had great vision, but I expect that they could not have predicted Kelly Johnson and the Lockheed Skunk Works creating the SR-71 in the 1960s – a Mach 3-plus aircraft capable of flying at the edge of space, or the team at Boeing in 1968 upscaling to the 747 capable of carrying in excess of 360 passengers and cargo on international routes.
Engineers live and operate in the world between known reality and unfettered dreams. Science fiction writers have inspired countless new technologies like satellites, computers, cell phones, space ships and more, but the engineers backed by investors brought them to reality.
New product project goals are largely set by people at the top who delegate responsibility for bringing those goals to reality. The visionaries are not the ones rolling up their sleeves to turn vision into actual product. Those visionaries are often government regulators, sometimes they are corporate executives, and sometimes think tanks and research centers. The visionaries challenge the status quo.
The captain says, “make it so,” and off you go to do it. The visionaries don’t let facts interfere too much with achieving the vision. A vision for the trucking industry is that zero-emission trucks are going to replace fossil fueled ones by 2030, 2035, 2040 — pick one. That is the stake in the ground. Now someone has to go make it a reality.
A common reaction to vision is to build a case that it is not possible to meet the target date. Significant energy can be wasted compiling facts about how long it takes to get steel for tools, how long it takes to test and develop a vehicle, how long it takes to get the market to adopt a new product — all sorts of facts based on prior experience. This is what I call bottom-up planning; using all the pieces of a project to build a plan, a schedule, a budget and more. This is approach is almost always overly conservative. One of my favorite quotes is, “Those that say it can’t happen need to learn from those doing it.”
At the other end of the spectrum, visionaries create top-down plans that start with a target product launch date, and then work backwards, force fitting program elements to fit. This approach is almost always overly optimistic.
The thing is, both the bottom-up and the top-down approach are fundamentally sound, but projects are living, breathing things that constantly evolve through the efforts and innovations of people. The void between these two approaches is, as a sage manager once told me, where the “miracles will happen” to bring the two worlds into alignment.
One of the truths of the truck engineering world is that deadlines tend to inspire creativity. Creativity is very difficult to predict. Creativity is not something that can be accurately programmed into a development schedule. It starts with accepting that the goal is possible, then figuring out how to make it happen. Countless examples are out there (one well known one was John Kennedy’s challenge to put a man on the moon in a decade), but you can look at Steve Jobs’ examples at Apple, or Elon Musk’s at SpaceX and Tesla, and many more. In trucking, the gauntlet has been thrown down to successfully bring zero-emission trucks to the market.
It is very difficult to plan for team synergies or individual inspiration and commitment. Planners often fail to recognize that people are more efficient or less efficient depending on how much they care about the goals. Putting in 60- or 80-hour work week because you believe in something will accomplish more than putting in the same number of hours because you are told to. A small group of committed, capable people often can outperform a larger group of people just doing their jobs.
A goal is always to work smarter not harder. However, setting and sticking to challenging schedules tends to force working harder in a smarter manner. And it’s not really about money. The level of funding is not necessarily an enabler. Having unlimited funds can lead to uninspired solutions, while having insufficient funds can spawn innovations and unforeseen partnerships. Sure, having a short schedule combined with a company blank check may get the job done, but it may not be all it could have been.
The debate about zero-emission vehicles hovers somewhere between “there’s no way they can do that” and “it’s obvious that zero-emission vehicles are the solution.” The passionate doubters often have valid concerns that can get lost in the emotions of arguing against ZEVs. The vocal proponents display a nearly unwavering faith in being able to get to zero emissions and often are overly optimistic about time frames and technical challenges. There are many people between these two extremes, and even a few who just don’t care.
Projects have to set performance goals, they have to estimate budgets, estimate costs, estimate timelines. It’s how projects get money and priority. Goal setting is part of the game. A senior executive sets visionary goals that the new product will be larger, more complex AND less costly than the one it is replacing. Like in a football game, the opposing side fights back with historical facts on how you can’t do that for cost that is lower than that of the current product. Facts and visions fight each other and eventually targets are agreed to that allow the project to be funded.
Too much vision or too much reality and the project likely will fail. Pushing the envelope too far or not far enough are risks in a competitive marketplace. Your new product has to compete against other teams’ projects, similarly, wrestling between vision and fact to create commercial success trying to avoid making the next great electric typewriter while someone in parallel is launching the word processor.
Getting a product out the door is not the same thing as being commercially successful. Companies that launched innovative new cabover products in the 1990s wound up stopping production almost as soon as they started. Those trucks may have been superior in many ways to the ones they replaced, but the market shifted and left those innovative cabovers behind.
As companies and governments are setting goals for market penetration of zero-emission vehicles versus fossil-fueled ones, some of these goals may seem unrealistic. At an event in 2018, I talked to regulators who were convinced battery electric long-haul trucks from Tesla and other manufacturers would be in production in 2019 or 2020. They even were creating incentives to help make buying those trucks and infrastructure possible. My experience with truck development programs said that schedule was not feasible, that it tends to take five years or more for new models to come to fruition. I went as far as documenting this in NACFE’s report Defining Production. I was not betting against the trucks reaching production, just arguing over the time frame. In 2023 many models of BEVs are now in production and in use through the efforts of motivated, inspired teams.
There were several opponents of BEVs in 2018 who strongly expressed that BEVs were not possible, at all. I was at one industry conference where an experienced diesel engine engineer laid out the rationale why BEVs were infeasible, too heavy, too costly, can’t get the power, etc.
Fast forward to June 2023, I attended Schneider’s ribbon cutting at their South El Monte, California, drayage facility where they are replacing all of their diesel trucks with 92 battery electric ones. For background on that, see the Schneider profile on NACFE’s Run on Less Electric – DEPOT website. There are nine other depots in the Run with a broad mix of truck classes. All of them are operational. These 10 sites are not unique. NACFE identified in excess of 100 sites covering several thousand trucks that were in the process of making the transition to zero-emission vehicles. They also are not limited to California.
In July 2023 I was on site at a Purolator facility in Richmond, British Columbia, near the Vancouver BC airport. That site had installed overhead charging inside the building at their loading dock so that 15 medium-duty package delivery trucks could charge overnight while being loaded or unloaded. The charging was simple, low cost, low power Level II chargers with innovative drop-down charging cables. There was almost no impact to floor space for the facility. Power draw was so minimal that the existing warehouse systems were capable of supporting the new loads.
The doubters who said these BEVs were not feasible are going to be challenged as the industry ramps up production and real fleets are implementing them. Each of the Run on Less sites had visionaries and capable, innovative teams to successfully bring BEVs into their operations.
Orville Wright lived to 1948. He got to see the development of intercontinental airlines, the introduction of the jet engine, the breaking of the sound barrier by an aircraft and rockets capable of reaching space. Each of those technologies came into being through someone setting challenging goals, combined with a committed group of people making it possible. Just as Wilbur and Orville had set the challenging goal of controlled, powered flight which they achieved in 1903.
Innovation, while hard to predict or plan for, is a significant force in technology adoption. That innovation is inherently tied to someone setting aggressive goals — like wanting to fly, wanting to cross the oceans non-stop by air, or wanting to transport freight without emissions. Let the innovators and the committed teams worry about making the miracles happen. They will.