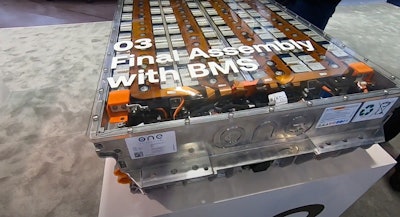
Our Next Energy (ONE) founder and CEO Mujeeb Ijaz recently explained at the Advanced Clean Transportation Expo how their new Aries lithium iron phosphate (LFP) batteries are made at their plant in Novi, Michigan.
Ijaz said Aries batteries offer a cost advantage over nickel manganese cobalt (NMC) battery packs and provide higher energy density. LFP batteries also reduce the risk of thermal runaway and avoid controversial sourcing methods associated with NMC batteries.
Aries batteries deliver up to 3,000 cycles and can be charged daily to 100% capacity without degradation. Testing in a Tesla Model S last June delivered 752 miles of range on single charge with a 204 kWh battery pack. ONE reports on its website that an Aries pack provided 150 miles of range during a test with a class 5 Motiv truck with a 3-ton payload.
Video transcript:
Mujeeb Ijaz:
Our battery company is launching this year these products, the Aries LFP battery packs, a 79 kilowatt hour version, and a 62 kilowatt hour version that go into many different types of class trucks. Class 3 up to class 6, and we're starting to even look at the Class 8 market. What we've set up in this display is an explanation of how we manufacture our battery products. It's all around our factory launching in Van Buren, Michigan, where we're assembling this battery pack in a very unique architecture. It's called high cell-to-pack. The cell-to-pack is 76% of our total battery system itself. What that reflects is the ability to bring lithium iron phosphate batteries to a competitive state where we can avoid nickel, avoid cobalt, and have the same or more range capability in a lithium ion phosphate battery.
Why do we care about LFP? LFP has had three advantages in the market all along. It's a cost advantage, there's a safety advantage, and there's a durability or lifetime advantage. All three of those are important to commercial truck customers, but what has always been a disadvantage is the range. We were able to overcome that problem. We now have a higher energy density than a nickel/cobalt battery pack, even the best in the world. This battery pack now exceeds the volumetric energy density of those nickel/cobalt batteries, including the best LFP batteries in the world. So that's giving our company an advantage in the market.
So what we're going to start with is an explanation of how our battery enclosure goes together. So we take an extrusion. This extrusion, which is a T extrusion, is the center spine of our battery pack, and we integrate this extrusion with a bottom cold plate. These have channels. This is where the coolant for liquid cooling flows into the battery pack. We put those together in a welded architecture, and as we weld this together, this forms an enclosure that's very strong, but also very lightweight and very energy efficient or energy dense.
As we then develop the next step in our manufacturing process, we're integrating all of the lithium iron phosphate cells by compressing them with their two castings. And then as we integrate these cells, we bond them with an epoxy to the cold plate. We then further improve the energy density by making a very low profile bus bar, and that bus bar is welded, which connects all the cells together. Then we have the voltage integration and the battery management here in the front. As that battery pack goes together, it takes very little footprint for our factory to produce 30,000 packs a year or one every seven minutes is our factory production capability.