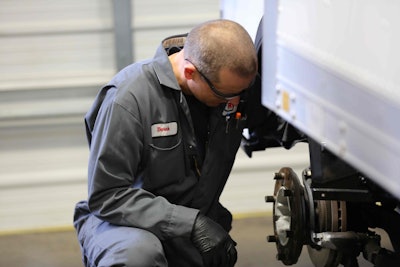
Note: This is the second of a two-part series on fighting corrosion. The first installment, “Truck washing a simple, effective method to fight corrosion” can be found here.
Corrosion is a silent killer, and a thorough inspection could be the difference in buying a quality used truck or an asset that’s a ticking downtime bomb.
Routine visual inspections that specifically look for signs of corrosion are an important part of any preventive maintenance program, but if you’re looking to buy someone else’s truck you’re at the mercy of their maintenance practices.
It’s important technicians address vehicle damage quickly – even something as seemingly mundane as a stone chip on a painted bumper.
“That is a very common place for corrosion to begin,” says PPG Commercial Transit Brand Manager Scott Colvin. “It doesn’t take much for a stone chip to crack through the paint down to the bare metal and once the rust starts, it will creep underneath, blister the paint up and start deteriorating the steel surface.”
In cases where component replacement isn’t necessary, Colvin says – at a minimum – affected, bare-metal areas should be coated with primer and/or paint to keep rust from getting worse over time.
Parts of the truck closest to the road are most susceptible to corrosion, making a visual inspection of the lower third of the unit vital. Left unchecked, corrosion will eventually eat through components on any steel structure.
“Such is the case for the wheel,” Colvin says. “It’s going to make thin areas within the structure of the wheel. If you let it go long enough, it could be unsafe. There’s brake components, brake lines, any part of the chassis or brake components, or the air-lines that are used to connect air brakes, all of that is susceptible to corrosion. If a line fails or some brake components fail, that could have bad results with accidents and injuries.”
In less severe cases, corrosion can simply add to downtime.
“Having rust and corrosion on the wheel end of the truck can take a 20 minute change of a tire and turn it into 40 minutes to an hour,” says Dave Latimer, Pilot Flying J vice president of shops strategy and operations.
Visual inspections, Latimer says, should include more than just scanning for red, rust-colored material because corrosion can also deform metal.
“It’s penetrating the metal and lot of times it will look swollen,” he says. “You’re looking for anything abnormal.”
“Our drivers are our first line of defense for corrosion,” adds Jim Dillon, truck assets manager for Gemini Motor Transport, noting drivers also perform daily inspections for signs of rust, electrical corrosion and flaking metal before the equipment is handed over to technicians who perform similar inspections as part of their PM cycle. “They’re constantly looking for any signs of it when they’re doing their pre-trip and post-trip inspections and they pay particularly close attention to the steering system, brakes, wheel ends, fifth wheel assembly and electrical connections.”
Wiring is especially susceptible to corrosion. Designed to keep moisture out, a hole in the plastic wire jacket out can actually trap corrosives and prevent them from being washed off.
“Any time that you have a wire that gets penetrated – the plastic wrap around it gets impacted or cut – that really allows an opportunity for [corrosion] start,” Latimer says. “Once it gets in there, it’s like a wick. It just spreads.”
A wiring check-up should be part of a pre-trip inspection and Latimer recommends plugs be cleaned with a wire brush before connections are made, and says it’s also helpful to use dielectric grease on connection points.
“When someone’s bobtailing, that connection is wide-open from the plug-in and corrosion starts in there and you’re going to get that flicker effect from that connection,” says Phillips Executive Director of Innovation Gerry Mead.
Another effective way to mitigate electrical corrosion is to use nylon components or fittings when possible.
“There’s a misconception that [nylon] is not as durable as metal, but that’s false,” Mead says. “All those can be sealed better they’re not susceptible to corrosion.”
Proper wire repair, Mead says, is also important.
“You can’t go around plugging in with a wire tester and poking it and breaking the jackets,” he says. “You have to have sealed butt connectors, trying not to have too many connectors.”