In the current trucking environment there are literally thousands of datapoints that fleets can capture and analyze. However, no fleet has the ability to analyze all the data that is available. Instead, each fleet must pick key areas on which to focus. Normally that data falls into safety and productivity buckets.
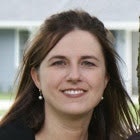
Here is a look at some things that are worth tracking.
Safety key performance indicators (KPIs) cover both driving and workplace issues.
Driving-related KPIs include:
- DOT Collision Rate — This KPI is used to determine collision frequency.
- DOT Inspections & Violations — This is used to determine a fleet’s road safety and unsafe driving measurements.
- Collision Reconstructions — This data helps aid insurance companies and legal agencies in the event of a collision.
- CSA Scores — This metric is calculated by the Federal Motor Carrier Safety Administration for every fleet.
Workplace related KPIs include:
- Injuries — This is used to determine the OSHA reportable injury rate.
- Spills — While these are infrequent occurrences, they are reported to the safety department and tracked from the time of the spill to disposal.
Productivity KPIs include:
- Preventive Maintenance Compliance — This is used to track units that are in compliance with their scheduled PM service.
- On Time Compliance — This reveals the percent of deliveries that are on-time, but also the reason for any late deliveries.
- Billing Data — This tracks mileage variances between planned and actual load miles.
- Miles Per Gallon — MPG is tracked weekly to monitor fuel consumption.
Many of these KPIs combine multiple points of data entry, application preferences and audience levels. All this adds complexity to streamlining data intake, data frameworks and delivering actionable reports. On the plus side, automating this process when possible reduces time spent on administrative report activities and increases employee availability for innovation, problem solving and promoting safety.
Engineering and automating the reporting process can be complex and require data reporting and data engineering skills. Business intelligence tools are available to offset the headcount needed for data project development in areas of report design, data aggregation, data transformation and monitoring.
While there are endless factors that can be monitored and analyzed, each fleet needs to choose the KPIs that make the most sense for their operation, including those that they are obligated to collect by governmental agencies.
While it sounds like a cliché, it also happens to be true: If you don’t measure it, you can’t improve it. Choose your KPIs based on the areas where you want to perform at a higher level. Your internal data gurus, coupled with business intelligence tools, can give you the data you need to take your business to the next level.
Dawn Dow is a member of Transervice Logistics’ National Logistics Technology team and has a combined 19 years of experience as an information technology and data professional in pharmaceutical, logistics, and construction industries. Her experience in application quality assurance and earning a Greenbelt certification in Lean Six Sigma ignited her passion for analyzing business system data to ensure process quality and data integrity for reporting and business insights.