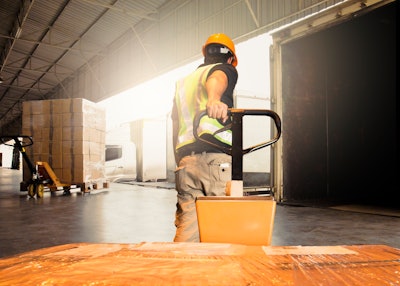
When you have a shipment, no matter how large or small, you want pickup, transit and delivery to go off without a hitch. Unfortunately, that isn’t always the case. Understanding the most common mistakes of freight shipping can help everyone get ahead and plan for success.
Improper packaging
Improper packaging causes an estimated $1.7B of goods damaged in transit annually. While 11% of packages arriving at a distribution center have some level of case damage, a large percentage of packages can avoid damage with proper packing. The odds of this damage occurring increase dramatically for shipments that travel over longer routes and require multiple transfers from truck to truck.
You may not be able to control the handling your goods undergo in transit, but you can control how well protected they are before they leave your hands, which all comes down to the technique in which you pack the goods.
Following your company’s freight-packaging guidelines, always use the proper materials for the items you’re shipping based on their size, weight, shape, fragility and value. To better protect your freight, start by palletizing your cargo, securing all loose products, wrapping your pallets in plastic and using a weather-proof seal. If you’re unsure how to properly wrap your shipment, ask your carrier how to ensure maximum security for both your goods and that of others who may be sharing the same truck.
Failing to recognize a shipment’s special needs
When ordering a shipment, remember to consider if it requires any special treatment. In almost all cases, if you fail to report something of this nature, the carrier will add a fee much higher than the agreed-upon rate. In order to avoid extra freight charges, consider the most common needs during the quoting process, which includes tailgate, appointment pickup or delivery, and any special handling of goods. Failure to note special services risks delays, loss, and destruction of your goods because you haven’t made the carrier aware of any specific shipping needs.
Skimping on insurance
Insurance is an important component that many people typically tend to opt out of to avoid an added cost. However, it’s a highly critical cost to shell out to help protect your goods, which can ultimately help save thousands of dollars in the long run. Freight insurance covers a freight forwarder’s liability for damage or loss to customers’ goods during transit. For a claim to be payable, the freight forwarder’s negligence must’ve caused the damage or losses.
Incorrectly classifying freight
When products move domestically in the U.S., a job LTL (less-than truckload) or TL (truckload) carriers generally handle, shipment spacing is at a premium. A 53-foot trailer can hold about 26-30 pallets, depending on shipment size and weight. Trucking companies save money by filling their trailers and, therefore, rely on a system known as a freight class calculator that provides them with an accurate pricing model. Understanding how to properly calculate a freight’s size and weight is imperative to avoid re-weighs and reclassing fees.
Use a freight-quoting system that makes it easy to calculate freight class, or skip the need for freight classes by shipping with exclusive use-style STL. Regulated by the National Motor Traffic Association, the National Motor Freight Classification or NMFC is the standard for comparing the many different types of freight and classifying them.
The NMFC also publishes minimum packing requirements, to enforce practical standards for protecting goods in transit and ensure that all cargo experiences reasonably safe handling and stowage. Finally, the NMFC governs the procedures for disputes or filing claims, as well as maintaining the terms and conditions of the Uniform Bill of Lading, a universally accepted contract of payment and receipt of completed delivery.
Paying to ship air when trailer space is empty
Every year, businesses spend an estimated $7 billion dollars on TL freight that ships with unused trailer space. This is equivalent to five out of every 100 truckloads moving empty. Truckload shippers often choose between paying for empty deck space and waiting to send their freight until it fills the truck to capacity. You can avoid this difficult choice by only paying for the space you need and moving freight in a multi-stop shared truckload.
At the end of the day, mistakes happen, but you can avoid them if you’re aware of common mishaps and areas to be mindful of. Avoiding these common mistakes can lead to overall time and money savings and can ultimately help the industry become much more efficient and sustainable.
Oren Zalansky is the CEO and founder of Flock Freight, a technology company that uses advanced algorithms to pool multiple shipments to fill trucks at scale through a new mode of shipping called shared truckload.