ABF Freight
Fort Smith, Ark.
Developed a tool to interconnect logistical data streams to manage shipments.
Streaming data
ABF’s Customer Shipment Manager makes light work of a cumbersome process
When a nationwide retailer plans to roll out new merchandise, thousands of transactions and communications will take place between the shipper, carrier and consignees. A complex stream of logistical data must be managed for the rollout to proceed on schedule.
More recently, another company rolled out a new line of household fixtures to its stores nationwide. The project involved moving product via containers internationally to a domestic warehouse for packaging. From there, merchandise was shipped to hundreds of locations simultaneously within a one-week timeframe. For every day of this project, ABF Freight provided its customer with multiple detailed reports about the delivery performance at each store.
ABF Freight always is evolving and expanding its slate of logistics activities. A critical part of managing complex projects is to coordinate and integrate data streams from multiple parties. After ABF management asked its IT department to develop a better method for doing this, a new Customer Shipment Manager application was developed in short order.
Instant analysis
While transportation companies seldom lack data, the greater challenge is finding the time and resources to mine this data, especially when complex projects with tight timeframes do not allow hours or days for business analysts or computer programmers to query separate databases to obtain critical information. A drawback of using electronic data interchange, Web portals and other common methods to exchange information is limited flexibility to respond to specific information requests.
“We are able to provide information efficiently, comprehensively and accurately in an expeditious manner.”
– Brent Dorrough, ABF manager of Customized Solutions
More carriers now are using data warehousing technology to consolidate data across various sources into a relational database used specifically for reporting and analysis. ABF Freight initially developed CSM in this fashion as a way to integrate customer service-oriented data.
As part of developing CSM, the IT department at ABF – a company known as Data-Tronics – created algorithms to find and filter critical data quickly for managing specific projects. The CSM application intelligently pushes the proper data to the proper people within ABF to make proactive customer service decisions.
CSM was field-tested during the fast-food restaurant project. The application had the flexibility required to receive and store supply chain data, and it also was able to accept varying data formats. But the database’s relational tables soon proved to be too cumbersome for expansion.
CSM then was redesigned to use XML to provide search engine-style speed for managing rapidly changing supply chain data. This enhancement enabled CSM to import data from more data formats, including Excel spreadsheets, and leverage ABF’s Web-based shipment tracking system to create a single source of logistical management data.
Today, at the click of a button, ABF is able to design logistical support packages quickly based on the specific needs of each customer. In turn, ABF customers gain real-time data that can be communicated in a variety of formats, including PDF files, EDI and Excel spreadsheets.
Early resolution
The CSM application is used mostly by the ABF ByRequest team, a centralized group of the company’s logistics specialists. The team operates within ABF’s Customized Solutions group and works with customers to manage shipping challenges.
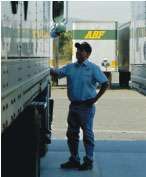
CSM uses templates to assist users in the setup process. Its features simplify the process for the ABF ByRequest team to acquire information they need internally and what they send to customers. The team can establish or refine the criteria quickly to identify problems in advance.
With CSM, the team can establish custom work crews for specific projects. If a coordinator needed to check the same five sources of data each day, the team could set the CSM program to monitor those data sources automatically and provide a single seamless data stream.
What once might have taken a business analyst a day to accomplish now can be accomplished in a matter of minutes. Moreover, coordinators are managing the project’s logistics using a single app rather than juggling various apps. The application puts everything ABF’s specialists need to plan, execute and manage supply chain data at their fingertips.
The retailer who contracted with ABF to deliver household fixtures to nationwide stores wanted to receive reports on a store-by-store basis. The details included the store manager’s name, what time the store was contacted by ABF for delivery, and if the delivery appointment was made at the specified time or if the manager chose a different time. The daily report also showed what time each shipment was delivered and if any quantities were short or damaged.
CSM also has improved communication between the customer service department and the terminals that route trucks, drivers and freight for pickups and delivery. If a shipment is running behind or is routed incorrectly, these and other problems will show up in advance.
“We proactively try to correct or resolve problems before they become an issue for the customer,” says Brent Dorrough, ABF manager of Customized Solutions. “If the shipment looks like it needs help, we are there to provide it.”
The CSM application gives management increased oversight control. Managers can analyze data to determine new ways to improve efficiency. They also can use the app to assign roles for various coordinators monitoring particular projects.
Creating a virtual glass pipeline for real-time shipment tracking and greater management control of logistical procedures are the project’s primary achievements. The CSM has made it easy to execute what would otherwise be a cumbersome process.
“We know we are able to provide information efficiently, comprehensively and accurately in an expeditious manner,” Dorrough says.
Innovators profiles carriers and fleets that have found innovative ways to overcome trucking’s challenges.
If you know a carrier that has displayed innovation, contact Jeff Crissey at [email protected] or 800-633-5953.