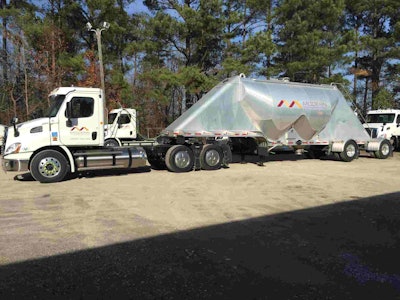
CCJ Innovators profiles carriers and fleets that have found innovative ways to overcome trucking’s challenges. If you know a carrier that has displayed innovation, contact CCJ Editor Jeff Crissey at [email protected] or 800-633-5953
In April 2013, Modern Transportation was among the first fleets to adopt the Cummins Westport 12-liter natural gas engine – straight from the assembly line. At the time, diesel prices were about $4.
The fleet’s experiment with liquefied and compressed natural gas-powered trucks has proven a success, both financially and environmentally. The results for emissions reductions earned Modern the SmartWay Excellence Award in both 2014 and 2015 from the U.S. Environmental Protection Agency. About 40 of the 3,000 truck carriers that participate in the SmartWay program receive this distinction each year.
However, the natural gas market has slowed due to the diesel price decline. While a $2.50 gallon of diesel remains equivalent to the price of natural gas, diesel-powered trucks are significantly more fuel-efficient.
Still, Modern continues to use natural gas as a cost-saving strategy by harnessing company data to make better decisions that have lowered its fuel and equipment costs.
“It’s taken work to do that,” says Patrick Cozzens, president of the Sewickley, Pa.-based fleet. “Part of innovation is hard work, being aggressive and being focused.”
Of the 350 trucks and 500 drivers in Modern’s dedicated fleet that transports bulk chemicals, minerals and materials, 30 trucks currently are powered by CNG or LNG. That share soon could increase depending on the results of a recent project.
Fueling decisions with data
When Modern began using natural gas in 2013, the company’s data was housed in nine separate databases. About six months ago, it deployed a data warehouse to unite its disparate sources of data and create new reporting and analytical capabilities.
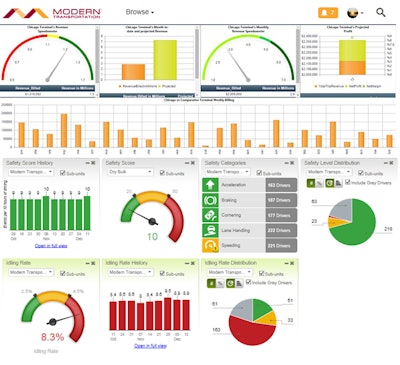
The data warehouse combines fuel data from three different sources, allowing executives and managers to identify variances and root causes for performance issues. This helps to quickly assess which strategies for improving fuel efficiency are working and which are not, Cozzens says.
If the fuel economy of tractors is less than expected, the root cause can be isolated to driving behaviors, mechanical issues, route characteristics or other factors. Besides using the data to maximize fuel efficiency, the company also can hold vendors accountable and collaborate with them to improve performance.
Bob Smith, director of equipment and maintenance, currently is working on a project to test a fuel-efficient tractor spec. The company’s terminal in Sanford, N.C., is the test bed for this project to compare diesel-powered tractors with CNG- and LNG-powered units.
The first truck to be tested, nicknamed “Super Diesel,” was put into operation in November. It uses a 15-liter diesel engine with a 12-speed fully automated manual transmission mated to a 6×2 single drive axle.
The forward nondriven axle in this 6×2 configuration is a tag axle that automatically raises and lowers according to real-time operating conditions. The truck also is spec’d with a number of aerodynamic features.
Smith also is testing both CNG and LNG tractors with a 6×2 tag axle and a Cummins Westport 12-liter engine with a 10-speed automated manual transmission. Smith says Modern is the first tanker fleet – and one of only two fleets in the nation – to have a natural gas-powered tractor with a 6×2 tag axle configuration.
The Super Diesel can achieve 8 mpg when pulling empty trailers, and 7.5 mpg overall. While the CNG- and LNG-powered trucks get the diesel equivalent of 6 mpg, they release half of the carbon and nitrogen oxide (NOx) emissions, Cozzens says.
The testing also includes a new spec for tank trailers with an automatic lift axle; this forward trailer axle applies more pressure to the wheels on the ground when loaded.
Besides using its data warehouse to analyze the fuel efficiency of this new equipment, management is looking at other cost-saving benefits by using this equipment across the fleet to extend tire life, Smith says.
Gaining deeper insights
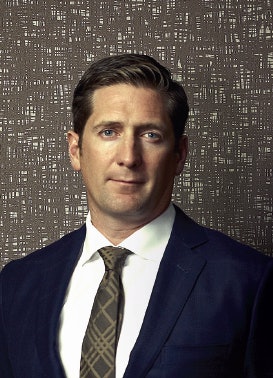
The data warehouse has proven to be a valuable tool for Modern to build its culture of innovation. “We challenge ourselves to get better every month, every quarter and every year,” Cozzens says. “Without that data, you are not able to do that.”
Management is able to monitor the profitability for every tractor, trailer and driver by doing projected weekly closings of the company’s financial reports to make faster and smarter decisions in near real time, he says.
One critical measure to maximize fleet profitability is payload weight. As a bulk carrier, Modern bills customers by weight and holds managers and drivers accountable. A daily report shows the opportunity costs for drivers who did not fill tankers to maximum capacity at quarries and other loading points.
Another example of harnessing data is predicting freight seasonality. Modern is determining freight patterns and lane volumes to proactively reassign equipment and drivers to different locations.
Every executive and manager uses a custom dashboard-style interface to the company’s data warehouse. Each dashboard is tailored to their areas of responsibilities and has real-time visibility of key metrics, including driver performance.
In every truck is a system that gives drivers real-time feedback by using various inputs to detect risky behaviors, most of which also impact fuel efficiency. An indicator on the dash changes from green to yellow and red according to the level of risk detected, and drivers can use a mobile app to review their scores in more detail.
The system provides detailed information for supervisors to manage driver safety. When scores change, “we have it and coach the driver immediately,” Cozzens says.
When implementing its fleet safety software system, Modern sent a letter home to the families of drivers to explain the new program and encourage spouses and children to ask drivers about their scores each day.
“The driver can pull it up on their phone through an app, and we publish their scores in the terminal so drivers see how they rank,” he says.
The company’s insurance provider has recognized its safety efforts for nine consecutive years, and Modern now is working with a data company to take a deeper dive into predictive analytics. The intent is to combine safety performance data with workers compensation and driver health data to identify areas of potential risk.
The project should give the company a more holistic view of its drivers, Cozzens says. It could identify those that may need treatment for certain medical conditions that could cause safety hazards, and it also help the company make more informed hiring decisions.
Another recent effort to improve driver safety during unloading events involves Modern’s DOT 407 chemical tank trailers that have a rear discharge pipe. The company has worked with vendors to spec a center discharge pipe to provide drivers more versatility while unloading at customer locations. It also began spec’ing a ground-level vapor recovery valve to eliminate the risk of drivers climbing to the top of trailers where those valves normally are located.
Modern first was recognized in November 2011 as a CCJ Innovator for its efforts to enhance its safety culture by using technology. Since then, the company has been able to harness all of its data and technology to make smarter decisions within a culture of innovation, Cozzens says.
For a recap of how CCJ’s 2015 Innovators challenged the status quo in the areas of safety, efficiency and more, click here.