CCJ Innovators profiles carriers and fleets that have found innovative ways to overcome trucking’s challenges. If you know a carrier that has displayed innovation, contact CCJ Editor Jeff Crissey at [email protected] or 800-633-5953.
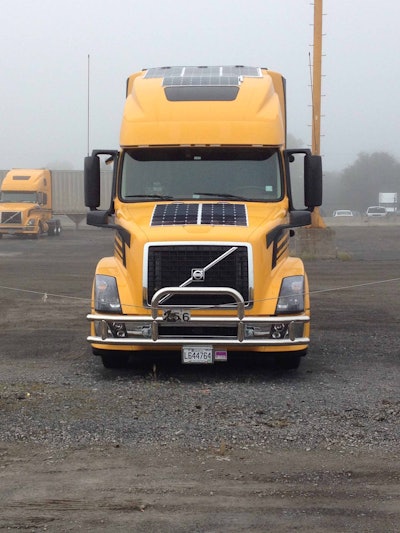
If you’re searching for a forward-thinking fleet north of the border, look no further than Rougemont, Quebec. This small town east of Montreal is home to Groupe Robert (CCJ Top 250, No. 37). The 71-year-old company, which began as a food transportation provider, has grown to become one of Canada’s premier trucking operations with 1,100 tractors, 3,200 trailers, 41 distribution centers and terminals and more than 3,300 employees.
Today, Groupe Robert offers general freight, specialized and bulk transportation services as well as logistics and supply chain management with 3.5 million square feet of distribution and warehousing space.
Spanning three generations, the family-run business has developed a reputation as one of North America’s most innovative trucking companies, creating many customer-driven solutions and experimenting with a variety of tractor and trailer equipment configurations to improve fuel economy.
Groupe Robert also has invested heavily in liquefied natural gas-powered tractors to lower its greenhouse gas emissions. Today, the company has 125 LNG trucks in operation, and the addition of these trucks led in part to one of the company’s most recent innovations.
Here comes the sun
Each of the LNG trucks in Groupe Robert’s fleet requires three battery-powered methane detectors – located in the engine compartment, cab and sleeper – to alert drivers and shop personnel to gas leaks.
If the LNG trucks are parked at a Groupe Robert facility, the vehicle’s battery system can recharge overnight as the trucks are refueled.
But for LNG trucks on the road and away from terminals, the methane detector’s around-the-clock operation can easily drain the batteries and reduce the available power for in-cab climate comfort controls.
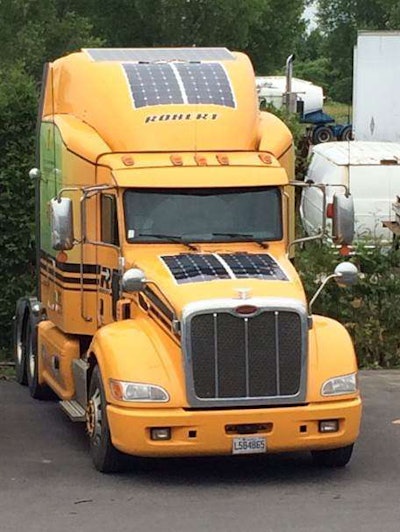
Simultaneously, the company was continuing a 15-year-long quest to find new ways to reduce idle time, cut costs and lower its carbon footprint across its entire vehicle fleet. By reducing excessive engine idling, Groupe Robert could save 2,000 gallons of diesel fuel per truck annually.
To reduce idle, the company previously used diesel-powered generators to charge batteries and provide electrical power for driver comfort accessories, but the noisy and maintenance-intensive systems still consumed more than a quarter-gallon of diesel fuel per hour.
In 2014, Groupe Robert began replacing its diesel gensets with a battery pack located behind the cab to power the fully electrical air conditioning unit and in-cab accessories, including microwaves and televisions. The move eliminated the additional fuel costs, but battery life was limited to six hours under normal hotel load.
“When a driver is sleeping with the air conditioning running all the time, the battery could drain before the end of the night,” says Daniel St-Germain, Groupe Robert’s vice president of material resources.
Seeking a way to extend the system’s battery life, Robert Frédéric, Groupe Robert’s director of material resources, turned to the recreational vehicle industry, where he found systems using 2-by-4-foot, aluminum-framed solar panels to charge battery packs.
Groupe Robert began installing the rigid 100-watt solar panels on the roof fairings and added four additional deep-cycle AGM batteries to store reserve power to supplement the original battery system.
“We had to cut through the roof fairings and make our own set of brackets to make the solar panels fit,” says Yves Maurais, Groupe Robert’s technical director for asset management, purchasing and conformity. “The results were so-so, probably extending the battery life by an hour or two.”
Maurais says the company’s “Aha!” moment came when it discovered smaller flexible solar panels that could conform to the shape of the roof fairing and tractor hood. “Because they were flexible, we could put as many as we want on the truck,” he says.
The flexible panels can generate an additional four hours of battery life and fully recharge in eight to 10 hours of normal daylight. Groupe Robert now installs six 100-watt flexible solar panels on each of its new trucks, riveting them to the roof fairing and tractor hood, and has retrofit its LNG fleet with the system to power the methane detectors.
St-Germain says the cost for its new solar panel charging system is comparable to its previous diesel genset equipment, but the elimination of fuel will result in a 3.5-year return on investment.
Just as important as the cost savings, Groupe Robert’s drivers now can remain comfortable for up to 10 hours in a climate-controlled sleeper berth.
“This lets drivers rest comfortably in a temperature-controlled sleeper compartment without the noise, pollution or waste that comes with engine idling,” says Frédéric.
Driving costs out of shop supplies
Groupe Robert’s innovative spirit doesn’t stop with its quest for fuel savings and equipment modifications. With a keen understanding that waste can be driven out of any aspect of a business, the company recently turned its sights on a small but costly problem – maintenance tools and supplies.
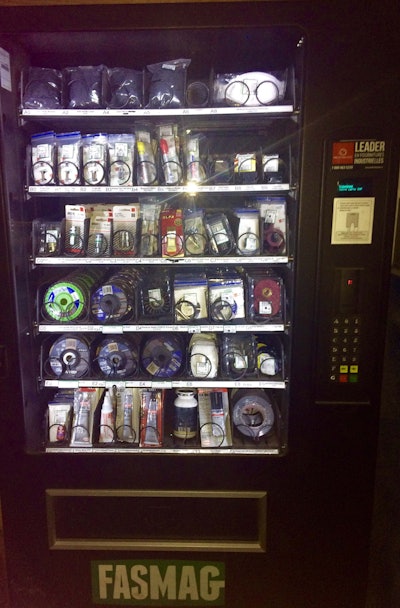
Management realized everyday shop supplies were being consumed at a higher-than-normal rate, but didn’t have a way of keeping track of who was using what.
“If a technician comes to us and says they need two cases of gloves because they’ve run out, you order them without asking questions,” says Maurais. “Then you realize some technicians were throwing the used gloves away every night and got a brand-new pair the next day.”
Four years ago, Groupe Robert collaborated with its local supplier to install a specialized vending machine at its Rougemont maintenance facility that staffs 30 technicians. Operating much like common snack vending machines, the new machine was stocked with 43 different SKUs, including gloves, batteries, hand cleaner, cutting discs and drill bits.
Technicians were issued unique ID cards used to dispense items from the machine and track technician usage of specific items. The machine’s management software also delivered reports to management.
“At the beginning of the month, I receive a report that tracks spend by employee and spend by item,” says St-Germain. “We now know exactly what people spend.”
Better still, the system allows the vendor to replenish SKU inventory automatically. “We only have to keep the machine in the shop,” St-Germain says. “The supplier restocks the machine every other week or so. We don’t even have to touch the machine at all anymore.”
Individual accountability for consumable shop items led to a significant cost reduction. In the one-year trial period, Groupe Robert reduced costs on the 43 SKUs tracked through the machine at its Rougemont maintenance facility by 50 percent, resulting in an eight-month return on investment.
Since the trial, Groupe Robert has rolled out the vending machines at all repair and maintenance locations and will expand the system to its warehousing and distribution centers. St-Germain says the company also plans to install machines in driver lounges to dispense items such as cleaning products, security equipment and apparel for its 1,300 drivers.