This is the second of a four-part series that looks at telemetry data as a maintenance tool in trucking, the information service providers seek to provide fleets, and how fleets use that information. The series is based on a survey conducted this spring by CCJ parent company Randall Reilly. The results can be downloaded here. Additional coverage in this series includes Maintenance telematics: New-age battleground for OEMs and the aftermarket, OEMs, aftermarket collaborate to fill gaps in telematic data, and What are fleets looking for from maintenance telematics?
The transportation telematics market is oversaturated with numerous tech companies on the scene trying to appeal to different types of fleets or specializing in a specific area like driver performance or compliance measures. Why, then, have original equipment manufacturers in recent years begun to develop their own telematics services when they could integrate with one or several of the many providers in the aftermarket?
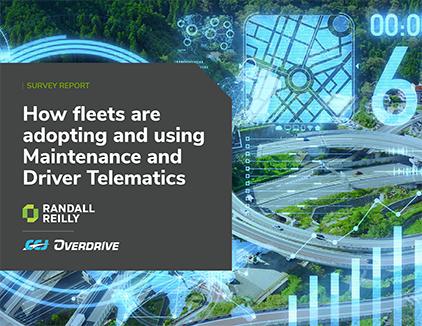
How are fleets and owner-operators using telematics? Find out with this comprehensive research from the editors at CCJ.
Download to access insights on what telematics solutions fleets/owner-operators are using, how telematics influences business decisions and more.
After all, aftermarket providers have been developing their platforms well before OEMs and have dedicated their entire business to this focus, whereas telematics is only a side or small line of business for OEMs.
“Aftermarket products were developed and offered several years prior to really becoming a substantial offering in an OEM environment … so there have been, in some cases, decades worth of technology developed in these areas. (Aftermarket providers) just have been around longer,” said Netradyne Chief Marketing Officer Barrett Young. “In an OEM environment, it's more that they are a jack of all trades, master of none situation where their biggest focus is providing opportunity integrated within the vehicles themselves versus being highly specialized in certain technologies. So for an OEM to be successful in leading the market and innovation, it will require them to be 10 times their size because they need to have very comprehensive departments handling all the different software and technologies that can be implemented. With aftermarket products, they've invested in truly being specialized in specific areas and being able to fund and support all the innovation that has to happen on such a very fast-moving timeline.”
According to CCJ parent Randall Reilly’s 2023 Telematics Survey Report, 45% of fleets are using a third-party or aftermarket telematics provider to gather maintenance-related data from trucks to improve uptime (68%), reduce costs by solving maintenance issues before they lead to major repairs (64%), and allow maintenance to be scheduled when convenient (48%).
While nearly half of fleets have turned to the aftermarket, 55% of fleets said they don't use a third-party provider. But that doesn't mean they're using their OEM's telematics solutions. Forty-two percent of fleets said they are still within the trial period of their OEM telematics services subscription and plan to renew, while 33% of respondents said they let it lapse without renewal, and 25% said they are still within the trial period but do not plan to renew. The majority of respondents (52%) said the reason they haven’t renewed their OEM telematics service is because they have other processes in place, and it’s redundant, while 24% said it was too expensive for what it does.
Turns out, there’s no one-size-fits-all solution for every problem a fleet needs to address, from safety to predictive maintenance and beyond, and while aftermarket providers tend to offer more data insights often backed by automation, there are some things you can only get from the OEM of your truck.
The most common difference between OEM and aftermarket telematics seems to be when it comes to fault codes.
“While a limited set of fault events can be accessed by most aftermarket solutions, only an OEM-developed telematics service can provide the broader set of detailed sensor data needed to perform a diagnosis for Virtual Technician and for prognostic solutions,” said Len Copeland, product marketing manager for Daimler’s Detroit Connect.
Virtual Technician, an in-depth, factory supported remote diagnostics program, is part of Detroit Connect’s uptime services, which also includes remote services like remote parameter updates and remote engine performance reports and safety services like Safety Event Viewer, Video Capture (the only native video recording service) and Safety Analytics, as well as eServices supporting the charging and operation of electric trucks.
Kenworth Connected Services Marketing Manager Brandon Singh said the same of TruckTech+, which monitors 800-plus engine and aftertreatment fault codes via factory installed telematics hardware.
“Engine and aftertreatment fault code data is similar to the aftermarket; however, the differentiating factor in Paccar Solutions is the labeled severity of each fault code (i.e. Stop Now, Service Now, Service Soon, No Action, In Repair),” Singh said. “Each severity level provides users with a quick diagnosis on how to handle each fault code efficiently in order to ensure the most uptime for the driver and company, while also protecting company assets.”
Another factor OEMs mentioned is their ability to update engine and aftertreatment software over the air through their factory installed hardware. Like Kenworth and Daimler, Navistar’s OnCommand Connection, Cummins Connected Diagnostics and Volvo Remote Diagnostics can also provide over the air remote updates.
Working remote
Averitt Express (CCJ Top 250, No. 26) Breakdown Coordinator Tim Gray​ said his company has built out its own transportation management system for tracking day-to-day operations, and primarily leans on Volvo's Remote Diagnostic capabilities for over the air updates.
"Years ago, if you had to do a software update on a tractor you would have to take it to a dealer or one of our shops. And, of course, that takes some time," he said. "Now, if you've got a good cell phone reception there for the tractor, it doesn't take five or 10 minutes."
Vikas Monga, director for Griffith, Indiana-based Charger Logistics (No. 191) – a fleet of more than 1,500 trucks – too has its own internal applications, but Monga agreed that the ability to push remote updates via Detroit Connect is among his favorite OEM capabilities because "it saves a lot of our time. I remember about four years back when we didn't have it, it was a pain to get the trucks into one of our shops and do the parameter change, or if you send to a dealer you pay that money. It's a huge cost saving and mostly the time. We use those remote updates very widely ... and then the best part is that we can do it as a bulk. We can choose a set of trucks and we can send a bulk update, or we can do it customized to a single truck if there's a concern with the driver or if there's any single application chain on a single truck."