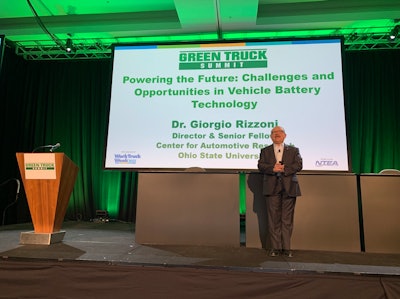
Bigger is not necessarily better when it comes to EV batteries and chargers, according to Dr. Giorgio Rizzoni, director of the Center for Automotive Research at Ohio State University, who spoke Tuesday at the Green Truck Summit at the Work Truck Show in Indianapolis.
Rizzoni said fleets need to lean more on understanding the duty cycles of their vehicles and then coming up with battery specs and charging solutions to optimize EV performance. In short, that doesn’t mean spec’ing the largest battery possible, nor the largest charger.
“Once you can charge at 50kW at home base, you have satisfied about 60% of [work truck] applications. You don’t necessarily need a large battery pack,” Rizzoni said.
A charger that size is a far cry from 350kW DC fast chargers that are fairly common at charging sites around the U.S., but speed isn’t everything.
“Fast-charging is not good for today’s batteries,” said Rizzoni, who added that moving forward batteries need to be better engineered “to withstand excessive charging.”
[Related: Cummins' CEO sees internal combustion waning as emissions regs tighten]
Having a larger battery also incurs greater upfront cost and increases vehicle weight, which cuts into max cargo capacity.
Slower overnight charging is also less costly than DC fast-charging. CCJ sister site Hard Working Trucks charged a 2022 Ford F-150 Lightning at home on a 220-volt outlet for 8 cents per kilowatt-hour (kWh) versus 32 cents per kWh at DC fast-chargers.
When spec’ing batteries, fleets will also have to consider climate. Both colder and hotter climates can shorten EV range, which may require a larger pack. The North and the Midwest, for instance, “go through some pretty significant weather variations,” Rizzoni said.
Vehicle type can also impact battery size options, according to Andrew Wrobel, director of auto and mobility at Escalent, who addressed the sold-out crowd in the JW Marriot’s ballroom following Rizzoni’s presentation.
Since powertrain batteries are typically installed between the chassis frame rails, short wheelbase vehicles may not be able to accommodate larger batteries.
“Short wheelbase may have packaging constraints,” Wrobel said. “These trucks are going to have the hardest time.”
[Related: Mercedes new electric eSprinter built to compete]
Battery selection for snowplow trucks and other four-wheel-drive trucks may also prove challenging given the extra space needed for additional drive train components.
Spec’ing that first EV battery is only the beginning. Fleets will have to look ahead to their next battery.
“How many battery packs will you have to buy over the lifetime of that vehicle?” Rizzoni said.
Fleets will also have to consider the role they play in battery lifecycle management. Powertrain batteries can be used in second-life applications like energy storage and ultimately recycled where Rizzoni said “progress is being made in recycling lithium batteries.” Cobalt, in particular, is one of the more desirable elements being pursued in recycling, Rizzoni added.
As far as a fleet’s obligations in battery lifecycle management, that’s still largely a work in progress.
“There are a lot of options out there that haven’t been figured out,” Wrobel said. “That’s one of the big questions: who’s going to own the battery moving forward?”