On Monday, June 2, a driver phoned Randy McGregor to report a problem: his truck was shaking and the “check engine” light was on. While they were still talking the engine shut down.
About two minutes later, McGregor received an e-mail showing the truck number, truck location, and that a critical engine shutdown had occurred.
McGregor, fleet manager for Transway, a 100-truck carrier based in Holland, Mich., clicked on a link to enter an online portal to do some research.
“I had a pretty good idea right away of what happened,” he said.
He then located a nearby dealership and towing service using the mapping tools in the portal. Meanwhile, a nearby dealer was reviewing the case file and scheduled a repair upon the truck’s arrival that afternoon.
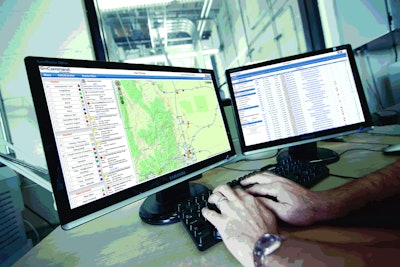
Transway uses an onboard computing and telematics platform from Omnitracs to capture and transmit fault codes to Navistar’s OnCommand Connection remote diagnostics portal. By clicking on a fault code from the main screen, listed next to the truck unit number, a document opens up to explain, in plain English, what the code means and what to do about it.
The document also has a set of questions to ask the driver to be more certain of the problem, McGregor said.
Transway operates International and Freightliner trucks with Navistar, Cummins and Detroit engines. Prior to using the OnCommand Connection, “check engine” lights could have meant anything. When drivers called the office McGregor had no information about what happened, and would often send drivers to a dealership, or have them towed there, to avoid catastrophic engine failures and breakdowns.
Trucks and drivers would then sit idle at dealers for possibly two or three days before a diagnosis was returned. Naturally, drivers might want to ignore the warning lights to avoid such a circumstance.
Conservatively, McGregor estimates the remote diagnostics portal saves the company $2,000 per day by preventing a breakdown or an unnecessary trip to the dealer that would result in lost revenue and additional driver expenses. In many cases, the non-critical fault codes can be handled at Transway’s own shop during the next PM schedule.
To view a quick presentation of how the portal works, click here.
How it came to be
McGregor discovered OnCommand Connect about eight months ago before it was officially available in February, 2014. The discovery came when he called Brian Mulshine to discuss some issues he was having with Navistar’s MaxxForce engines.
Engine lights were coming on and were forcing the company to stop drivers without knowing what the problem was. “It was getting frustrating,” he said.
Mulshine, director of service performance and technology for Navistar, had the foundation of the portal already in place and gave McGregor a quick introduction. Instantly, McGregor saw the problem was nothing more than an ambient air temperature code. “It was no big deal. We could keep drivers moving,” McGregor realized.
Navistar developed OnCommand Connect as an open platform to receive telematics data from any source. It had already developed a proprietary telematics system called Aware. And, like Freightliner and Volvo, the company could have marketed its own diagnostics platform for International trucks.
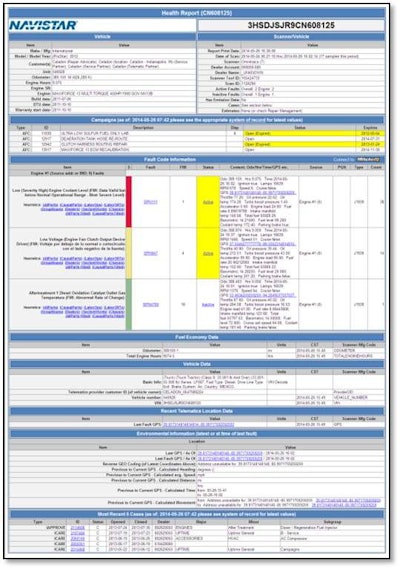
Instead, Mulshine pursued an open approach by working with some fleet customers, including Jim Coffren, vice president of maintenance for Hirschbach Motor Lines. Early on in the development he asked a major telematics company to provide Navistar with the fault codes it was collecting from vehicles for all makes and models. “Why would we want to give you that data?” was the response. Mulshine countered with a question of his own. “Do you want the OEMs to decide who the telematics vendors are?”
Developing its own telematics platform or partnering with an existing provider would make Navistar a major competitor in the telematics market, he explained, just like Freightliner has become by partnering with Zonar Systems to create a product offering.
Conversations with fleet executives gave Mulshine confidence that the open platform was the best way to go. They did not want to pay extra or use more than one telematics platform to manage a mixed fleet of vehicles.
“We went a different route,” he said. “I don’t know many fleets that operate only one brand of truck. You’ve got to be able to do the whole fleet.”
The OnCommand Connect portal receives fault codes and other telematics data from Omnitracs, PeopleNet, XRS, Telogis and other major providers of mobile fleet management systems through standard XML-scripted communications.
The fault codes use standard SAE protocols which make it possible for Navistar to have a common diagnostics platform. The portal also displays the locations of all OEM dealerships and fleet shops, not just International dealers.
Transway’s Randy McGregor said the portal has been helpful to detect issues with Freightliner trucks, for instance. Some of the radiators in its Cascadia tractors have developed a leak which triggers a low coolant fault code. The only advantage for using the portal to monitor Navistar equipment is having access to more online service manuals and documents, he added.
Hirschbach Motor Lines has seen a 34 percent reduction in downtime by using the portal to stay ahead of developing problems, Coffren said. The Dubuque, Ill.-based carrier operates 565 trucks with Cummins, Detroit and MaxxForce engines and 900 refrigerated trailers.
“Things don’t typically go down the road and fail. You see a progressive failure. OnCommand Connect is able to aggregate so much data that you see the patterns for how the failures of trucks progress,” he noted.
Since the launch in February, OnCommand Connect is now monitoring fault codes from 40,000 vehicles from all manufacturers, said Mulshine, who expects to have about 500,000 trucks online by next year.
Navistar continues to add new capabilities to the portal such as analytical tools that show the amount of time that certain types of fault codes take to repair, based on statistical data, and the cost of parts and labor. It is also developing mobile apps for fleet managers and drivers to monitor the health of vehicles.
As to why a truck OEM would develop a tool that helps companies manage all vehicles in a fleet — not just those with its emblem on the hood — Mulshine offered this explanation. What remote diagnostics platform do you think PeopleNet, Omnitracs and other telematics providers are recommending to their customers?
“They view Daimler as a threat,” he said. “We are calling on customers today we have never called on. Our sales arm has increased tremendously.”
With the successful launch of the OnCommand Connect platform, Mulshine recently left NaviStar for another job opportunity to head up innovation for Rush Enterprises which operates the largest network of heavy and medium- duty truck dealerships in North America.
Working out the bugs
Like any new software system, the OnCommand Connect portal has some areas that need to be tuned up.
“Some of our operations people say that they’ve been getting an inordinate amount of false positives where the system says there’s an issue but when they hook up the truck they don’t see it,” said John Reed, chief information officer of AIM NationaLease. “We expect issues like this in the early stages of any new product but they’ve been a great partner to work with and we’re confident these will be quickly resolved.”
AIM NationaLease operates a leasing and rental fleet with thousands of trucks and a dedicated logistics fleet. The company has been using OnCommand Connection for about two months to monitor the health of vehicles with engines from Cummins, Navistar and Volvo.
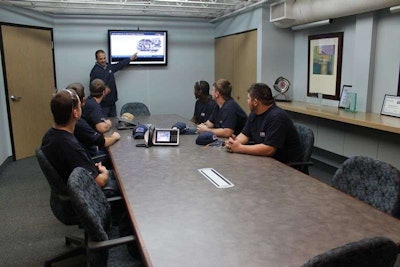
“What this does as a product is it puts everybody into the same playing field,” added Terry Dimascio, executive vice president of AIM NationaLease. “Navistar is taking everybody’s service book and cross referencing materials and sending information to us in the same format, every time. We are getting the same message from all of our trucks.”
Reed said he knew the system had tremendous potential the first time he saw a demo using the company’s own telematics data supplied by PeopleNet. The company also uses a low-cost telematics system from Geotab to capture data.
At the very moment the demo was finished a critical fault code appeared that required immediate action. The driver was instructed to verify that his engine light was on. Once verified he was instructed to take the truck to the nearest dealership for correction.
“This avoided a costly tow, substitute unit and lengthy down time,” Dimascio said.
AIM is currently working with Navistar to create an application programming interface (API) that would eliminate the need to monitor its fleet through the portal as its main features would be directly integrated into its maintenance software.
AIM created a system called RescuePro to manage its equipment breakdowns. Through the API, the codes would flow directly into RescuePro to alert the appropriate people — based on the severity of the code — and automatically initiate work orders in its maintenance management system.
A serious fault code would alert the company’s 24-hour rescue team to call the driver and immediately react, he said. AIM currently uses the web portal to monitor 100 trucks in its dedicated fleet and trucks leased to 30 customers.
“We are seeing critical codes every day and we are dealing with them every day,” Reed said.
As International continues its turnaround project, fleets are encouraged by its successful and potentially “game changing” work in remote diagnostics and fleet management.