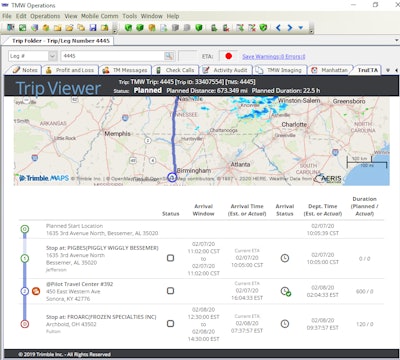
With the final compliance date for the electronic logging device (ELD) mandate in the rearview mirror, a number of technology suppliers are focusing on the trip planning process for drivers.
Hours of service, traffic, weather, truck parking and many other variables have made trip planning a complex problem to solve.
New developments in transportation technology are mirroring apps used by consumers to navigate through traffic, public transportation and air travel schedules.
Workforce demographics is another factor driving the need for motor carriers to give drivers better trip planning tools. Millennials are now the largest segment of the workforce, and as younger workers enter the transportation industry they expect the technology they use at work to mirror the technology used in their personal lives.
Creating round trips
Motor carriers of all types continue to focus on creating better routes that simplify the driver’s trip planning and are supplementing these strategies with technology.
Dry van truckload carrier Cargo Transporters, Inc., has 11 fleet leaders that each manage between 50 and 55 drivers. The company’s load planning process focuses on giving drivers out-and-back trips.
“We do not do a lot of triangles; we’re a head haul – back haul carrier,” said Jerry Sigmon, chief operating officer. Drivers have familiar routes and work for the same customers. Those that live in the Carolinas have opportunities to pass through their homes during the work week.
“It works out well for the driver and for the customer,” Sigmon said.
The fleet leaders know what types of loads and lanes drivers prefer, and the company’s open-door policy gives drivers a chance to meet with managers whenever they pass through the company’s Claremont, N.C. headquarters.
As part of the dispatch process, drivers get a backhaul with an outbound load as early as possible to help with trip planning. When drivers have a round trip they can better plan when and where to take required rest breaks, Sigmon explained.
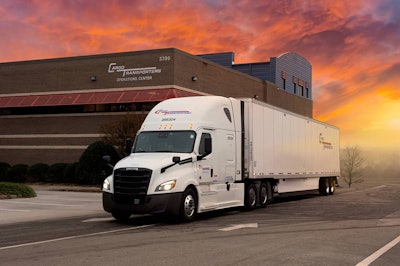
“We are always trying to improve our pre-plans, so our drivers know as quickly as possible what their next load is going to be,” he said.
When dispatching, fleet leaders communicate any known dwell times for “live loads,” where Cargo Transporters does not have spotted trailers for drop-and-hook operations. This communication helps drivers plan ahead. If a load has an expected delay of six hours, for example, a driver might decide to take a 10-hour off-duty break at a shipping or receiving location, Sigmon said.
Drivers can view and respond to all dispatch assignments using the fleet’s mobile communications platform or by using the driveCT mobile app.
The onboard platform has a navigation app that shows drivers company-approved fuel stops along their routes. The app also gives turn-by-turn directions to shipping and receiving facilities. Cargo Transporters identifies and inputs the exact GPS coordinates into the navigation app based on route analysis and driver feedback.
“We try to do what we can inside our walls,” Sigmon said, adding that has allowed drivers to be as efficient as possible and “maximize their earnings and home time.”
Taking out stress
Giving drivers accurate information about their routes, such as how long they will spend on activities like driving, loading and unloading, helps alleviate job stress and keeps the focus on safe driving.
A number of fleet management systems have mobile apps for their drivers or field technicians to quickly access important job information on the fly, such as customer locations and information and specific delivery or job-site instructions.
“As they’re working at the job site, they can record notes, photos and signatures to help inform future conversations with the office and provide proof of service,” says Bridgette Brown, product success manager at Verizon Connect.
“With the mobile app, technicians can see a list of jobs assigned to them for the day. Plus, they can view upcoming jobs assigned to them for up to a month in advance. By using the map view, workers can easily find the location of jobs in relation to one another, and quickly access directions using apps on their device,” she says.
Marigolds & Onions, a Toronto-based catering and event service provider, optimizes driver trip plans each day using a routing software from Paragon Systems.
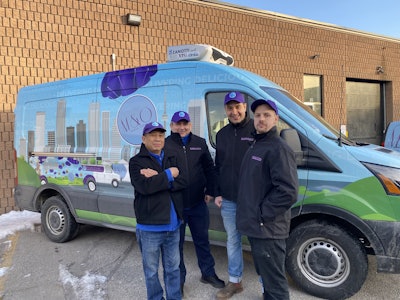
Prior to implementing Paragon in the summer of 2017, the company had been planning delivery routes manually for its fleet of 11 cargo vans. Fleet planners divided up daily orders from customers into routes, allotting drivers 30 minutes of travel time between stops.
Once deliveries were complete, planners used a manual paper-based system to schedule next-day pickups for used items such as dishes and supplies. Copies of the delivery manifests from the previous day were plugged into current-day routes for drivers to pick up after they had made deliveries at nearby locations.
With this manual system, a number of pickups were falling between the cracks, said John Valente, director of operations.
Marigolds & Onions receives an average of 100 orders from customers each day. The Paragon system pulls in orders from its ERP system and builds optimal route schedules for both deliveries and pickups.
Drivers return to headquarters two or three times each day to drop off used equipment and pick up new orders. The orders are loaded onto racks.
Paragon accounts for how many servings fit on each rack, and the number of minutes it takes drivers to unload a rack. With these details – and the software’s street-level database – the system accurately calculates departure and travel times for each stop on routes, Valente said.
Drivers are less stressed today because their routes have accurate times allotted for travel, for delivery and for pickups, Valente added. The company is also saving money on fuel and vehicle maintenance by reducing mileage, and saving labor costs from having less dead time between deliveries.
“The flow is extremely accurate,” he said. “Now, drivers know exactly what they are doing all day long.”
Drivers also feel like they have control over the routing. Schedulers can tailor routes in Paragon to avoid streets with road construction, for example, based on driver feedback.
Valente said the company plans to add a mobile driver app for presenting electronic invoices to clients at delivery to capture a signature. The fleet also plans to implement a vehicle telematics platform and integrate the GPS data with Paragon to analyze planned versus actual routing, as well as capture reefer temperatures and driver safety data, he said.
Capturing driver intent
A number of software tools can optimally match drivers to loads and create routes, but where many of these tools fall short is they do not account for changes that drivers want to make to the plans, such as where and when they prefer to take mandated rest breaks.
Last September, Trimble Transportation announced a Driver Trip Planning feature for its TruETA route planning tool that captures driver input to calculate more accurate time estimates for arrivals.
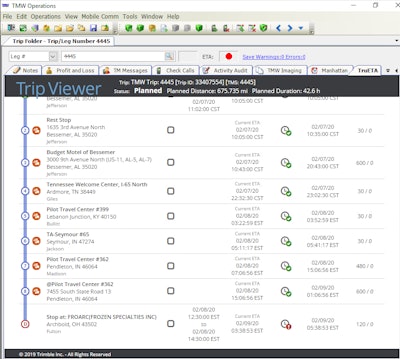
TruETA pulls data from systems in the office and vehicle to dynamically recalculate the ETAs of loads in progress. The ETAs are recalculated each time a position update is received from a fleet’s mobile communications system.
Motor carriers that use the new Driver Trip Planning feature can give drivers visibility of their trip itineraries in the TMWGo mobile app. The itinerary shows the locations and time of day for planned hours of service breaks. It also predicts arrival times for all delivery points.
The trip plans calculated by TruETA assume drivers will use the maximum 11 hours of drive time on their clocks and stop for the minimum amount of time required for rest breaks. However, “that’s not how drivers operate,” said Jay Delaney, Trimble Transportation senior director of product management.
Delaney said Trimble’s industry data analysis shows drivers typically use 9.5 hours out of the 11 they have available to drive in each duty cycle.
Within the app, drivers can update their trip itinerary if they want to extend their breaks at any location from a timeline view of all planned stops for their trips. The app also gives drivers a map view of their current route with traffic and weather overlays.
If a driver wants to take an 11-hour rest break instead of the minimum 10-hours, the system will recalculate the driver’s ETAs for the remainder of the itinerary to show what effect the change will have, Delaney said. If a driver wants to make additional stops they can input that as well and see how that impacts their ETAs.
A driver may not want to drive five hours straight like the plan shows. The driver could change the itinerary to stop every two hours, for example. This and other updates to a trip plan give the dispatcher real-time visibility of how the driver is executing according to plan.
The ETAs are constantly being recalculated. If a driver gets stuck in traffic, or is delayed at a customer, fleet managers can be alerted if the ETA falls out of range to make plans to prevent service failures, he said.
Trimble Transportation has plans to integrate the TMWGo app to telematics devices that fleets use. The company also plans to add a new tool for drivers to input predicted time available (PTA), showing what time they will be available for the next load once they are empty.
“For the next evolution we will take that into consideration,” Delaney said.
Giving drivers a choice
A strategy used by some motor carriers to help drivers with trip planning is letting them choose from a pre-selected list of loads.
McLeod Software has a “feasibility engine” in its LoadMaster transportation management software. When fleet managers make a load assignment, the engine determines if the driver assigned to the load has hours available and checks for other conflicts like time-off requests.
LoadMaster has the capability for fleets to offer company drivers and contractors a choice in loads. The loads can be pre-screened for feasibility and for driver preferences, said Dustin Strickland, senior product manager at McLeod Software.
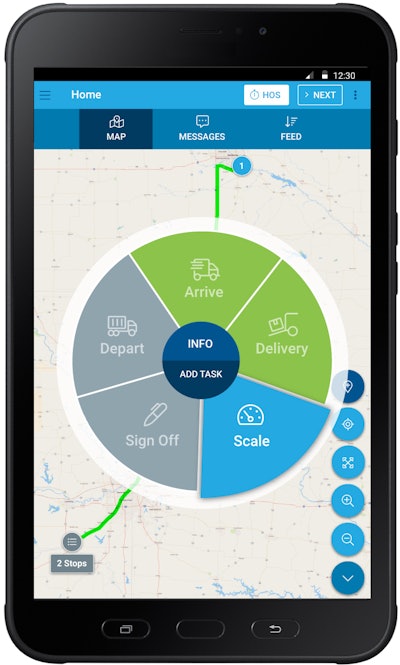
The load offers are visible through the McLeod Anywhere mobile app. Drivers can respond to load offers through the app or through their fleets’ web-based driver portal. McLeod Software is also exploring additional features that could make the trip planning process more interactive for drivers and fleet managers, said Mark Cubine, vice president of marketing.
Many of the new developments for driver trip planning center on improving the flow of location-based information. Omnitracs’ new mobile fleet management platform, Omnitracs One, has a “contextual based workflow” tool that fleets use to customize driver workflow by location.
The driver interface has circles that show all of the jobs that drivers need to complete at each stop and drivers push buttons on the circle to go through the workflow, said Gary Blohm, vice president of sales for Omnitracs.
The jobs might include filling out a delivery form or doing an equipment inspection report (DVIR). Omnitracs also has a team of data scientists working on a project designed to help carriers remove the friction of detention times. The company is building a database for tracking detention times at billions of locations that are visited by 600,000 trucks subscribed to its platform.
ELDs have narrowed the margin of error in trip planning. Even simple mistakes by drivers and fleet managers can lead to service failures and exacerbate job stress. New fleet management technology aims to remove the guesswork and make the most of time that is available.