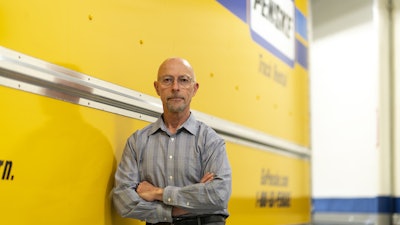
Mike Hasinec has spent the better part of his life looking for a house, but for the last 41 years, he’s known exactly where his professional home has been.
One of three boys born to a working family in Laurence Harbor, N.J., Hasinec was active in school sports – namely track and football – and the Scouts, where his mother served as a den mother and his father a Webelo leader.
“Because my parents worked, my brothers and I became pretty self-sufficient,” he said. “We learned to cook, iron, sew. We learned a lot of life skills.”
But at the age of 13, with his father’s employer – a local newspaper where he managed distribution – embroiled in a strike, the Hasinecs packed up and headed south.
“He just didn’t like the issues that occurred with his friends,” Mike recalled. “My dad literally quit his job with nothing lined up. We sold our house, and we moved to South Carolina.”
Neither parent claims to have made the decision with clairvoyance.
“My parents actually had some friends that lived in New Jersey in our little neighborhood, and they had moved to South Carolina several years prior to us moving, and they talked about how much they liked it, the way of life,” he said. “My parents, just on a whim, said, ‘You know what? Sounds like a good place to move.’ ”
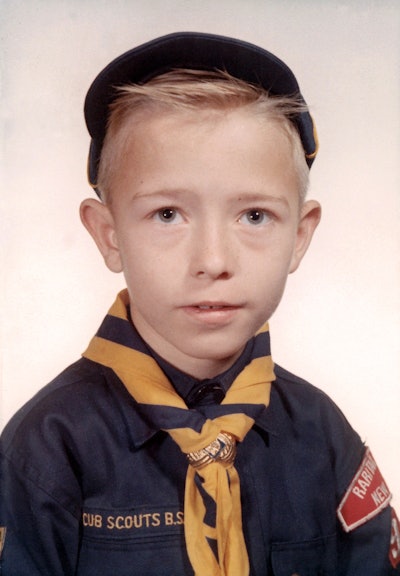
Leaning on their fondness for scouting, the Hasinecs were avid campers, a life skill that would serve them well over the course of the 700-mile move, as they wound up living in their 19-foot travel trailer for several months while the family worked to get settled into new jobs.
A freak knee injury during a softball game ended young Hasinec’s sports career, but the family began to settle in their new home in the Palmetto State, and by his teen years, Mike had developed an affinity for cars.
“I was always somewhat mechanically inclined,” he said. “My youngest brother had a Volkswagen [and] over-revved the engine. We all know what happens when you over-rev the engine. I built my first engine in my brother’s Volkswagen.”
Hasinec was particularly drawn to hotrods, such as his brother’s 1966 Plymouth GTX, and got himself a 1969 Road Runner, “which required a lot of money to keep up,” he said.
To raise funds, Hasinec joined his parents in the working world, but that wasn’t an unfamiliar place.
“When my dad worked for the newspaper, my first job was delivering newspapers when I was like 10 years old,” he recalled. “Back in those days, you delivered house-to-house, and you literally collected the money from your customers by knocking on the door.”
He joined his mother on the sewing line at Her Majesty Industries in Greenville.
“I actually sewed on production, and I got a job in the warehouse where my dad worked at Woolworth,” he said.
Those jobs were good to keep the Road Runner rolling, but Mike – a science and math whiz who finished two levels of algebra in one year – was setting his professional sights higher.
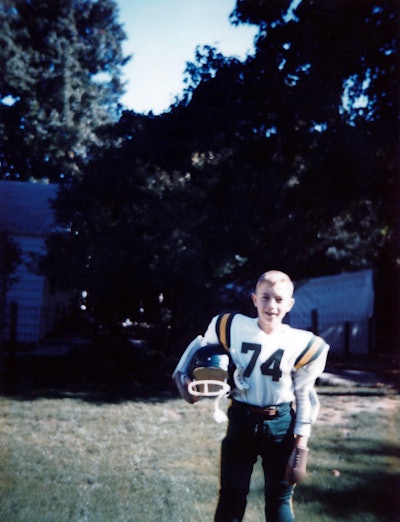
After graduating from Mauldin High School in 1976, Hasinec enrolled at Greenville Technical College in the mechanical engineering program, taking classes at night while working during the day, hopeful to one day land a job with one of Detroit’s Big Three auto manufacturers.
“That didn’t last very long,” he said of his engineering aspirations. “I didn’t like the teachers, and the hours were kind of getting to me.”
About six months later, Hasinec transferred to the school’s diesel technology program.
“I always liked being mechanical, and I thought this could be a field I would be interested in,” he said. “It was very closely related to the mechanical engineering piece, because I’d be working on heavy equipment. I was interested in engineering, because my whole life, I’ve just liked to fix things and understand how they work. I never envisioned being a bridge-builder or a manufacturer-type thing. I was always interested in automotive — really the design of cars, engines, things along those lines.”
Mike credits his then-girlfriend, and now-wife Karen, for the quick and easy change of course in his career.
“There was just something about my wife that motivated me to land on a kind of home life, and I figured the diesel class would be a much shorter period of time to accomplish versus the mechanical engineering piece,” he said. “I didn’t have the patience after I met my wife to wait four years, think about getting married and settling down.”
Settling down and settling in
Mike and Karen married in 1977 and had a son, Michael, the following year. During that time, Hasinec worked two jobs – a gas station at night and Greenville Builders Supply on weekends and nights – while balancing school work during the day.
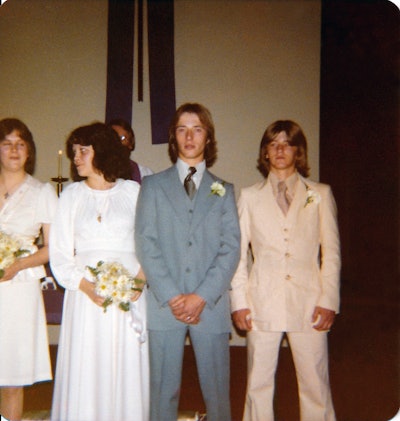
He graduated the Heavy Equipment class at Greenville Technical College in 1978, and “then I got lucky and landed Hertz Truck Rental at that time.”
On May 11, 1978, Hasinec started his career in trucking as a fueler, filling up, washing and detailing Hertz trucks.
“I got very lucky, because our district service manager at the time allowed me to start working in the shop, just doing little odd jobs — fixing lights and doing some preventive maintenance,” he said.
He steadily climbed his way to the shop floor, eventually progressing to technician and then to lead technician in charge of the second shift.
In 1979, Hasinec was given an opportunity to work in a Greenville Hertz shop that serviced Coca-Cola, and he was taken under the wing of a man he calls his first mentor: Gus Hill.
“Gus really was the shop foreman, but he ended up turning over all the administrative duties to me, because he just didn’t like doing them,” Hasinec said. “That was my entry into management. At the time, I just didn’t know that. I learned a lot of back-office skills and things like that — to learn how to run the facility from a [profit-and-loss] standpoint, and inventory.”
Meanwhile, the Hasinecs welcomed a daughter in January 1984 and had grown tired of living in various apartments.
After spending the days in Coca-Cola’s truck shop as a now-Hertz-Penske employee, Hasinec picked up a night job working directly for Coca-Cola, loading trucks and driving a forklift in the same facility.
“I did that for an entire year,” he said. “We were able to pay off credit card debt and save up some money to buy our first house.”
The Hasinecs bought their first house in April 1984, but the family of four wasn’t able to enjoy it for long when Mike was presented with an opportunity to help open a new Hertz-Penske shop as its maintenance supervisor in Lexington, Ky.
“We moved, right after buying our first new house, four or five months later,” he recalled.
Moving would be a recurring theme for the Hasinecs, as Mike methodically climbed his way toward the top of now-Penske’s maintenance division, but the opportunity to lead a new facility, including six technicians, was too good to pass up.
In Lexington, Hasinec was able to flex some of the management and back-office muscle he’d learned in Greenville, but he also figured out that sometimes being the go-to guy comes with inconvenient repercussions.
“In the winter of ’85, that January – my daughter’s first birthday – we ended up having a blizzard. We had no water and no power in our rental house, so I brought my wife and kids to the shop that Sunday so I could get all the vehicles started so they could go out on the road,” he recalled, noting that was also the first time he crossed paths with Roger Penske.
“It was a very important account at the time,” Hasinec said. “We were one of the first fleets running the new Mack MH613 with the four-valve head, and we had issues with parts, so that’s why Roger came out and visited.”
Movin’ on, again and again …
In 1985, and with the Hasinecs wanting to get closer to family in South Carolina, they packed up for move No. 2, this time bound for Charlotte, N.C., where Mike had been named district service manager.
“I had a large group,” he recalled. “Business was booming in Charlotte. We expanded to quite a few facilities and towns within a 100-mile radius.”
In 1986, the Hasinecs bought their second family home, this time in Gastonia, but sticking around to enjoy that level of success would be short-lived again, as Mike’s ascent through the ranks at Penske led him to Jacksonville, Fla., in 1990 — the family’s third move in six years.
“There was an opportunity to improve a low-performing location, and I saw this as a chance to kind of show myself,” he said.
And show himself he did.
After only three years in Jacksonville, Hasinec was named area maintenance manager, handling two states and upward of 50 locations and charged with oversight of maintenance procedures and policies.
About 24 months later, Hasinec was given the opportunity to return to the Carolinas in the same capacity but in a larger territory that covered South Carolina, North Carolina and Virginia.
“I jumped at the chance,” he said, noting the area finished first in corporate rankings for several consecutive years.
By the turn of the millennium, Hasinec was asked by Ken McKibben, then Penske’s senior vice president of maintenance, to take on oversight of five states east of the Mississippi, all the western states and Mexico as field vice president of the western United States — which meant moving yet again, this time to St. Louis.
“That was a very tough year, because my daughter was going to be a junior in high school,” he recalled as the family prepped for their fifth move. “I think most people can understand what that was like and that conversation.”
Two-and-a-half years and 400,000 American Airlines miles later, McKibben moved Hasinec to Penske’s corporate office in Reading, Pa., to lead the company’s Six Sigma efforts, which led to another difficult conversation with his only daughter.
“She just graduated from high school,” he recalled. “We literally were enrolling her in the University of Missouri when we decided to move again.”
For the last 17 years, the Hasinecs have called Pennsylvania home, capping a streak of six moves around the United States and countless changes of address.
“It’s the longest I’ve ever lived anywhere,” he said.
The company man and the family man
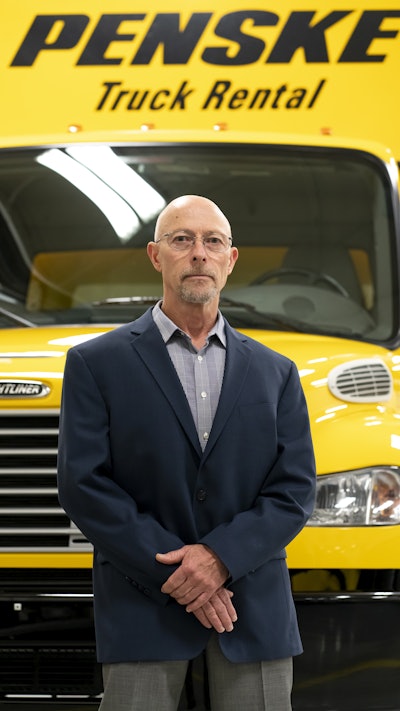
Among all the moves, the Hasinecs spent several periods separated for long stretches of time. For example, while Hasinec was transitioning from area maintenance manager in Florida to a similar role in North Carolina, the family remained in Jacksonville for almost a year while Michael readied for high school graduation.
“I was only going home every couple of months,” he said.
And in those long times apart, the balancing act of being one of Penske’s rising stars and being a dad was a challenge.
“Not having that daily activity with the kids, sometimes there’s a little bit of tension,” he said. “I remember coming home one time, and my son had let the grass grow as high as my knee, and we had a pretty serious conversation that probably shouldn’t have taken place.”
Hasinec worked to make sure what home time he did have was quality time, and he also was able to sneak in stints as a youth baseball and basketball coach.
Bouncing around the United States with kids in tow, he said, did have a positive impact on the family, although it wasn’t obvious at the time.
“An unforeseen benefit is that, to this day, we’re a very close tight-knit family,” he said. “Both of my kids live 15 miles away.”
Both also work for Penske. Michael, following a stint in the Army, now serves as technical development trainer, while Megan is vehicle maintenance coordinator.
Hasinec was married at the age of 18 and started working for Penske at 19, and with the exception of part-time work he held down on nights and weekends, Penske – by way of acquiring Hertz – has been Hasinec’s only employer.
“Some people grow with a company, and some people are a key reason for the company’s growth,” said Gregg Mangione, senior vice president of maintenance for Penske Truck Leasing. “I would put Mike in that latter category.”
“It’s been the only real job that I’ve had my entire life,” Hasinec added, noting that in May he will have been with the company 42 years. “I grew up with the organization,” and growing up together has, he added, enabled him to “learn with the organization and grow with the organization. I’ve been very fortunate. I came in at a time we were expanding. We had lots of growth, acquisitions taking place.”
More than four decades with the same company is almost unheard of, but Hasinec deflects much of the credit for his staying power to his colleagues because, he said, people such as Holly Gerke, Erich Pfahl and Eric Whiteash – with whom he has worked with for more than 15 years – have made it impossible to leave.
“If you work with people that you really love from a relationship standpoint, it’s kind of hard just to say ‘I’m going to toss that to the side,’ ” he said. “And I learned by moving so much in my career that the grass isn’t always greener on the other side.”
Still, 40-plus years with the same company doesn’t happen by luck or by love, and Hasinec said sometimes it just all comes down to rolling with the punches.
“My dad was always a dedicated hard worker, and I feel like I’ve been the same for the Penske organization, so that’s definitely one attribute I brought from my father — how hard work can get you further ahead,” he said. “All any organization owes to you as an associate is an opportunity. What you do with that opportunity depends on one person — the person that you look at in the mirror each and every morning.
“I’ve never been afraid to roll up my sleeves, get engaged and get dirty,” he continued. “That’s what this business is all about.”
Now Penske’s vice president of maintenance, Hasinec has been involved in or birthed many of the company’s prominent maintenance initiatives, including technology projects such as ServiceNet and PartsNet, and “a lot of our internal proprietary systems to manage our facilities and service.”
Penske’s internal technician certification program was born from an idea in 2005 and a year later was the first in the industry to become certified by the Automotive Service Excellence/National Automotive Technicians Education Foundation (ASE/NATEF).
“Ever since, that program has just grown into something we just never fathomed,” Hasinec said. “Today, we have 1,500 technicians enrolled in the program. We’ve had folks go from Tech 3s to 2s to 1s, and in our world, Tech 1 is the most senior tenured associate — the folks that typically can do it all.”
Hasinec also saw a need to develop an internal training organization that since has ballooned to 40-plus people and is overseen by Gerke, a longtime team member who helped develop the program. This past year, Penske increased the number of technical trainers in the field to 32 — two per area.
“When you look at the organization that Holly now directs, we do our own videos, we have our own video-audio person, we write our own technical literature, we have an instructional designer so that when we develop courses, we have a desired outcome — how we’re going to measure that and maintain it,” Hasinec said.
Hasinec’s fingerprints are on many Penske projects, but he noted two that stand out personally: the building of Penske’s Technology and Education Center (PTEC), and the development of a network-wide diesel particulate filter (DPF) distribution program.
PTEC, a 7,400-square-foot facility in Reading, has become a hub for Penske’s training and serves as an in-house validation center for new tools and technologies before they are rolled out to the company’s managed service centers nationwide.
Penske’s DPF centers – which now total four across the United States and Canada – facilitate a remanufacturing program of sorts that allows the organization to have inventory on-hand for a DPF exchange when a truck comes in for regular service.
With DPF-related expenses “going through the roof” in 2014, Hasinec huddled with senior management to run a proof of concept to show that having DPFs on the shelves – basically a stocked part at its shops – would reduce expense and downtime. As part of a beta test, Hasinec worked with a local supplier to get DPFs with various nameplates to support 20 locations in the mid-Atlantic area.
“We created our own little ‘milk run’ where we delivered DPFs to those 20 locations based upon PM scheduling, as well as when the DPF needed to be exchanged,” he said.
Hasinec said that over the course of several months, the data showed the group’s execution rate was over 85%, and with results in-hand, the initiative moved into the pilot phase the next year, with Penske renting a facility and purchasing its own DPF cleaning equipment for the Northeast region. The project, he said, saved upward of $500 per unit.
“When you did the simple math at the time with our fleet size, it was millions of dollars (in savings),” he said, adding the company then green-lit the opening of two more DPF centers with air, bake and aqueous cleaning capabilities.
“Last year, we cleaned 37,000 DPFs,” he said.
More than just cleaning the DPF internally – Penske remains the only company undertaking such a practice in-house – Mangione said Hasinec has put in place methods to learn from what they see when the filter is removed, which has affected everything from how the company specs its trucks to idle time.
Mangione said many of the innovations that Hasinec helped put in place with his team have positioned Penske as a marketplace leader in terms of technical expertise. He lauded Mike for being “a couple steps ahead” of the industry in solving problems that all fleets share.
A certified Six Sigma Black Belt, Hasinec served two terms on the ASE Board of Governors and holds numerous OEM certifications in engine, electrical, HVAC powertrain and braking systems. He sits on numerous customer councils, including the product councils that developed Eaton’s Procision and Endurant transmissions and Cummins’ X12 engine. He currently sits on Daimler’s Electric Vehicle Council.
A familiar face at TMC, Hasinec and Penske helped bring the first aftertreatment station to the SuperTech competition in 2017.
At home on the road and at Penske
That knee injury that derailed Mike’s sports career eventually took with it another favorite pastime: riding motorcycles.
“I enjoyed getting on the open road, going on long trips. I probably averaged somewhere around 8,000 miles a year on my motorcycle,” he said, while noting he’d made it to just about every signature motorcycle show, including Daytona, Laconia and – the mother of them all – Sturgis. “In every one of those, I rode from Point A – in this case Pennsylvania – by myself. Getting on that bike gave me a release and the ability to clear my mind.”
A couple of years ago, Mike replaced his motorcycles with a more knee-replacement-friendly travel-trailer — a throwback to his childhood and another tool that brings his tight-knit family a little closer together.
“I bought a pickup truck, I bought a fifth wheel, and we wanted to have our grandkids to experience camping, so I bought a fairly large 33-foot fifth wheel [trailer],” he said. Along the way, he was able to pass along his love of the outdoors to Karen, whom Hasinec said as recently as a few years ago would have defined camping as “a Hampton Inn versus a Marriott.”
“Six months later, we traded that in for a 40-footer that slept like 10 people,” he added, noting that since then, the family has upgraded again, this time to a motorhome.
Among the perks of being in senior management, Hasinec said, is now getting to watch associates grow into their careers, just as Gus Hill, Ken McKibben and others were able to watch him.
“There are people out there that, if you show them how to do things, are hungry for knowledge and information,” he said. “There’s people in this company who worked directly for me or indirectly with me as technicians who are now district service managers, area maintenance managers, even VPs. It is good to share. When you see people grow and become successful, there’s a lot of internal reward.”
“He has shown incredible compassion for people,” said Gerke, who started her career as an administrative assistant before leading the company’s training program that she helped to install. “The one thing I love about Mike is he is caring, he’s incredibly fair [and] consistent. He knows his people very well.”
Getting to know his people, Hasinec said, was a learned skill, and given the chance to go back earlier in his career, he said he would coach his younger self to be less headstrong.
“Understanding what inspires people, understanding the diversity of people, understanding what motivates people differently,” he said. “I kind of learned that later in my career than I would have liked to. I wish I could have learned what I learned later in my career earlier on when it came to motivating and interacting with people and how to get them to all pull the rope in the same direction.”
"Tips from the Pros" is sponsored by: