CCJ Innovators profiles carriers and fleets that have found innovative ways to overcome trucking’s challenges. If you know a carrier that has displayed innovation, contact CCJ Editor Jason Cannon at [email protected] or 800-633-5953.
Cross-border freight is a highly transactional business, especially in the less-than-truckload sector.
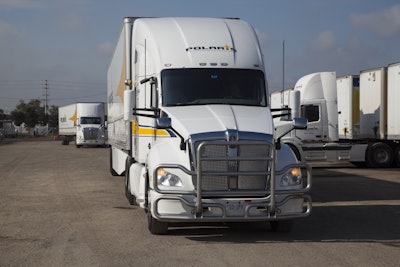
Each order has documents and data to process before a truck arrives at a border, from a bill of lading to load confirmations and the back-and-forth emails to gather product dimensions and descriptions from shippers to create a customs invoice.
“Every order is its own life form,” says Dave Cox, chief executive officer of Polaris Transportation, an LTL carrier with headquarters in Mississauga, Ontario, Canada.
Polaris Transportation devised a way to automate the customs process and free office workers from clerical work to focus on more productive and rewarding activities.
The effort began by researching a technology, robotic process automation (RPA), as the possible solution to reduce labor costs and increase data accuracy. RPA uses software algorithms as self-learning “bots” that are programmed to do tasks across multiple applications, just like humans.
Laying a digital foundation
Each year, Polaris does business with up to 6,000 customers with its fleet of 120 tractors and approximately 280 trailers that move more than 300,000 orders a year to and from the U.S., Cox says.
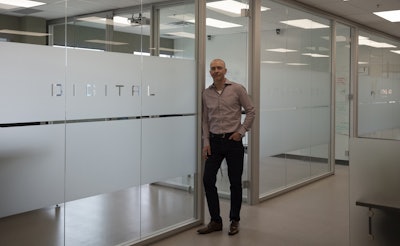
To grow the company, Cox doesn’t want to invest in back-office manpower to process more freight orders. He is also concerned about the human factor of spending a workday punching keys.
“How enjoyable is that to an individual?” he says. Adding more manpower in a good economy could also potentially create human collateral in a downturn. “That didn’t make sense to me.”
Polaris had already been using “non intelligent” document processing technology with optical character recognition (OCR) to extract data from paper and electronic forms automatically, says Dave Brajkovich, chief technology officer. The technology worked well but required significant intervention by staff to manage repetitive processing.
Brajkovich had been serving as a board member of Polaris Transportation when he and Cox discussed the possibility of using RPA technology about two years ago. Brajkovich was the applications developer at a financial firm in Toronto using RPA. He saw firsthand the benefits of taking mundane, labor intensive processes out.
Cox invited Brajkovich to work full time at Polaris, and soon after the company selected a platform from WorkFusion to be the RPA foundation to develop its own intellectual property for “intelligent process automation” of customs work, Brajkovich explains.
“It was a significant undertaking as far as having to lay the foundation of software and hardware, but that was probably the easiest part,” he says. Going through each layer of business logic and “tagging” data elements and processes for bots to manage was more difficult. It took about four months before a system was ready for the production environment.
Carving out efficiency
In September 2018, Polaris launched its new RPA platform for order entry. The company accepts many modes of orders from customers, from its web portal, email and even faxes. “For anything coming through that has a person touch it, we trying to put an automation piece in,” Brajkovich says.
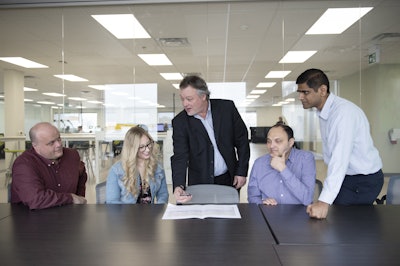
Office workers use a single screen, a WorkFusion-based application called a “control tower” to manage data inputs and corrections that the bots identify as exceptions. From the control tower, any data that needs to be corrected is fed to internal and external business systems via application programming interfaces (APIs).
Polaris has carved out about 85 percent of the customs process flow to automate by using robotics to decipher emails, read content and data from electronic paperwork. The quality of data has improved significantly too.
“We are not retouching the orders,” he says, with data moving to its enterprise systems and packaged up for customers in an efficient and accurate manner.
The overall time savings in order entry is two or three hours a day, he says. With the previous document management technology, the company started as early as 6 a.m. in order to clear orders through the customs process by 5 p.m.
Now, all of its daily processing is completed by 3 p.m. or earlier, and “we have time to manage exceptions,” he notes. The amount of overtime has decreased by 30 to 40 percent, and its bots are preventing quality issues that might otherwise cause freight to not be cleared at the border.
Another benefit, Brajkovich says, is that Polaris has data analytics on every process. The bots report on everything they do, from how many orders they process to the error rates.
“We never had that visibility before. It is giving us real insights to be a better customer service provider,” he says.
Creating career opportunities
Implementing technology to eliminate tasks done by humans can be unsettling to office workers. Polaris communicated with employees in advance to explain what the technology would do and provide new cross-training opportunities, particularly in customer service, Cox says.
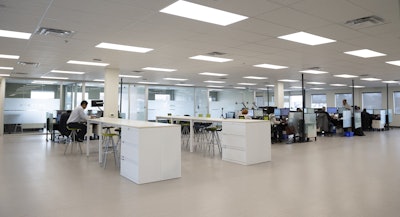
Employees can develop their careers by moving into different departments from third-party logistics to warehousing and distribution. “We are trying to develop people and talent,” he says.
Previously, up to eight people in the office were touching orders on a full-time basis. Now only two people have the job function as others have been repurposed and re-skilled to fulfill roles with more human-to-human interaction.
“When workers have their heads down and working on tasks they are not seeing the full picture. They have a tendency to get tunnel vision,” Cox says.
By freeing workers from doing mundane, repetitive tasks the company has more customer relationship management resources that are “picking up phone and talking to people.”
“We are trying to do more of that, so our clients are getting the attention they need,” he says.
The Digital Laboratory
Soon after Polaris Transportation started investing in the RPA technology, the company created a new addition in its office space to be a “think tank.” This vision for the area, called a Digital Laboratory, is to bring together executives and technology workers to “digitize” Polaris, Cox says.
Three quarters of its office building focuses on moving goods to market through warehousing, distribution and cross-border assets. The other quarter of the office is a Digital Laboratory that Cox describes as a “clean, positive space that would be something different than supply chain.”
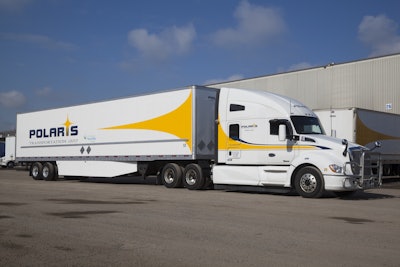
Polaris created a new company for the new office wing called NorthStar Digital Solutions.
Northstar owns the intellectual property for RPAs, which are for the transportation customs process. The sister company serves Polaris Transportation by providing efficiencies that are not found in other software systems, Cox says. Through its partnership with WorkFusion, the company also is selling and supporting RPA technology for transportation and logistics companies as a software-as-a-service.
In addition to providing customs automation technology, the company is developing systems to automate accounts receivables, payables and other areas.
Cox says NorthStar Digital Solutions is currently working on RPA projects for Polaris in accounting and will soon be turning its attention to load planning. The company also has been working with IBM to develop a Blockchain platform for transportation.
The goal of the Blockchain platform is to be first to market with a “distributed ledger” on a centralized hosted environment that will be easy to use and make Polaris and its other customers easy to do business with, Brajkovich says.
With its coming Blockchain developments, Polaris and NorthStar have positioned themselves to provide services that go beyond RPA to integrating business models throughout the supply chain.
“[Blockchain] will allow for the common sharing of business transactions between partners, shared services providers, competitors and clients – used by organizations and consumer-end users who are looking to receive fast, efficient, secure and cost-effective service,” he says.