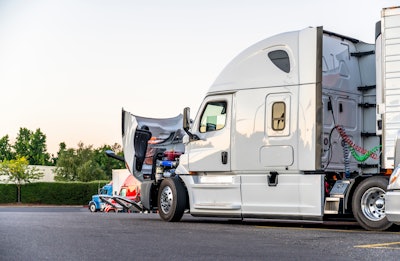
When mining what might appear to be unlimited data, it’s important to focus on three key areas: Reducing the average age of your assets by balancing the replacement cycle; Developing the most advantageous asset specification for your applications; and establishing accurate reporting
Equipment-related purchases have a large bearing on cost, and the age of the truck has a direct correlation to repair and maintenance costs. Put simply, older trucks will tend to require more maintenance and therefore cost more to maintain and repair, depending on the type of warranty purchased at the time of the vehicle acquisition.
However, newer trucks, which will cost more, may be equipped with better safety equipment aimed at mitigating collisions, and these safety systems can be more expensive to repair should they get damaged.
Using the data you collect from your preventive maintenance combined with your running and unscheduled repairs, you can calculate your cost-per-mile based on the model year of your assets to determine by model the costs associated with your equipment.
This approach will give you a better understanding of the costs you are incurring based on the equipment application and will help you transition out of equipment that is costing you more to maintain.
By lowering the average age of your assets, you will maximize savings because you will be able to replace the assets that are the most expensive first while you improve vehicle uptime.
Maintenance and repair data will also show you abnormally high-cost trends that you should analyze and leverage in the component specification selection process on your next truck order. The goal of this exercise is to reduce failures, which lead to much higher operating costs.
For example, fuel consumption comparisons of different powertrain configurations on similar routes will provide you with data necessary to evaluate the configuration that performs best for your duty cycle. Setting idle shut down timers and speed limiters will also provide a safer environment but reduce operating costs.
The data analysis also will uncover specific issues that you can discuss with your OEM of choice and truck dealer in order to determine if there are ways to spec your vehicle to reduce operating costs. This could be spec’ing a specific battery or even adding an additional battery to reduce the no-start issues you might be having.
One thing to note, you don't have to change the spec on every vehicle. Select a few units on which to test the new spec or new technology. This allows you to monitor how the spec change impacts vehicle performance and total cost of operation. If the change is beneficial, you can upgrade the rest of the fleet accordingly. If not, you can revert back to your existing spec.
For the data to be useful, you must have accurate reporting, and that means building your work orders in a way that captures exactly what work was done. Vague comments or lack of detail will not help you make informed decisions.
Follow the rule of three C’s: Complaint, Cause and Correction.
It is equally important that the work be coded properly using VMRS codes. These codes will pinpoint the system that is malfunctioning and help you identify specific categories where there are ongoing issues.
For example, you might find a significant number of repairs are being made to aftertreatment components. If your repair orders are coded properly, you will be able to identify if the problem is with the EGR valve, EGR cooler, turbocharger, etc. By identifying repetitive problems, you will gain insight into vehicle specification and preventive maintenance program shortcomings.
Properly built and coded repair orders will help you determine what you would like to monitor going forward, which can help you spec your equipment properly.
You can look at a specific component code failure and run reports that show at what interval you are replacing a specific component. For example, your report may show that you are replacing starters on a particular type of truck at 175,000 miles. As you go through your investigation you see that these trucks are used in on-highway applications with low idle percentages — 6% with annual mileage of 125,000. Using this information, you can seek warranty redress and you also have identified a part that should be replaced on your spec due to poor quality.
You can gain valuable insight from the maintenance and repair data you collect and can leverage it to improve the overall operating efficiency of your fleet.
Matt Copot is vice president of maintenance at Transervice Logistics Inc., and is responsible for overseeing the company’s warranty, purchasing, quality assurance, fleet systems and training programs. Copot began his career in the transportation industry in 1996.