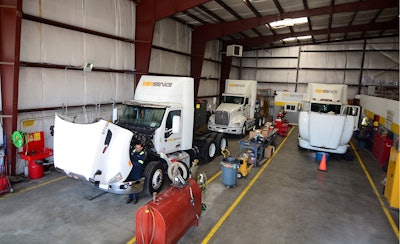
Given the current difficulty getting new trucks, it is even more important than ever to focus on preventive maintenance (PM) if you hope to get maximum life out of your assets.
When setting up your PM intervals, work with your OEMs to get input in their recommended service intervals for your specific equipment. Your oil drain intervals will change based on your application, and if your equipment is seeing higher MPGs there is a direct correlation to extended oil drain intervals.
Remember there are three kinds of maintenance: 1) Preventive maintenance is based off of predetermined service intervals. 2) Predictive maintenance focuses on condition-based repairs and using oil sampling to determine proper oil drain intervals. 3) Unscheduled maintenance is really repairs that are required between your scheduled PM services.
You will want to monitor scheduled versus unscheduled repair ratios to measure the effectiveness of your PM program. The goal is to get to a 70/30 split between scheduled and unscheduled. You also need to monitor your maintenance workload. How many units are currently due for PM service this week? How many are expected due the following week? How many PM services were completed last week?
Service intervals can be lengthened in conjunction with predictive maintenance practices. Predictive maintenance allows for a more proactive replacement of components to maximize uptime and reduce costs related to unscheduled maintenance.
However, changing PM schedules – or moving to a predictive maintenance model – is predicated on having data. You need a database to accurately track costs, warranty and parts pricing, along with other key performance indicators (KPIs) that are important to you. It is a good idea to focus your KPIs on safety, maximum uptime and reducing lifecycle costs.
Having accurate reporting on mileage/hours/days on each piece of equipment allows you to properly schedule equipment in for PM service. In doing this you can match your current workflow (units needing service) versus current manpower hours in the shop. You can adjust as needed to ensure all the work gets completed. Given the current parts shortage, scheduling and workload become even more critical as you need to ensure the parts are in stock for the forecasted workload. Uptime will be optimized if you know your workload and the corresponding parts needed for the repair.
Today’s technology can be leveraged to give you needed information. Your telematics devices allow you to track idle time, fuel economy, fault codes, fuel consumption, over-speeding events and other safety events. Fault codes will identify areas of opportunity in the fleet specification as well as assist with your predictive maintenance analysis.
Bluetooth technology can also be used to perform software updates and many electrical and mechanical repairs can be diagnosed through your OEM and or ELD portal using the vehicle’s fault codes.
All of this should help reduce repair times and get assets back on the road more quickly.
Fleet maintenance can be more challenging if you do not have an in-house maintenance facility, which can be staffed by your own technicians, or you can contract out your shop and have outside technicians do the work for you under a dedicated contract maintenance program.
However, should you choose to send your trucks to a third-party maintenance provider, remember they are profit-driven and their goals may not align with yours. If you are going to use a third-party maintenance provider, it is important to establish service level agreements with each one and to have clear expectations about the work they will perform as well as knowing the fixed labor and parts costs.
Technology means you can have a wealth of data about your assets, which you can then use to set proper PM schedules. When vehicles are properly maintained you are able to maximize their life and lower your total cost of operation.
Matt Copot, is vce president of maintenance at Transervice Logistics Inc., and is responsible for overseeing the company’s warranty, purchasing, quality assurance, fleet systems and training programs.