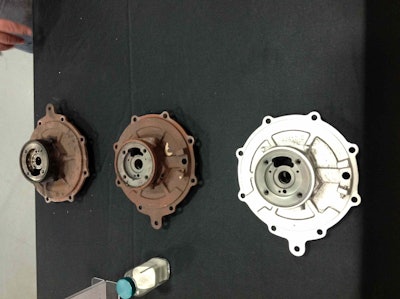
When shopping for a new product, you typically start with the stores you know stock the highest quality products at the lowest cost. What if these same stores sold “remanufactured” products at a 20 to 30 percent discount? Would you consider these as valuable as a new product?
Every time you fly commercial airplanes you trust your life to remanufactured products. In fact, one of the most important components has likely been remanufactured several times. Airlines are required to replace their jet engines every 1,000 hours.
Rather than purchase new engines, airlines exchange used cores for remanufactured engines that are as good — and perhaps even better — than the original. The same is true with heavy-duty diesel engines.
Using advanced recovery processes, diesel engine parts can be restored to original performance and warranty levels but sold back at a fraction of the original purchase price. Besides the cost-saving incentive, remanufactured parts preserve natural resources and conserve energy.
“We see remanufacturing as the ultimate way to reuse material,” says Stefan Kurschner, president of Detroit Reman, one of the largest providers of remanufactured products for on-and off-highway power systems. Last year the company processed 30,000 tons of core material into finished goods.
Detroit Reman, a Daimler Company, recently provided CCJ and other members of the trucking press a tour of its largest remanufacturing facility in Tooele, Utah. The Tooele facility is one of six ( five in the United States and one in Mexico) that specialize in restoring high value components such as turbos, engine heads and blocks, piston rods, and differential axles to the original OEM standard.
The tour demonstrated that remanufacturing involves much more than inspecting, washing and reassembling parts. It involves recovery of original cores, complete disassembly, and adding material through a “flame sprayed” welding process. It also includes precision resurfacing of components and a controlled assembly process.
The Tooele facility’s main product line is turbos. From June, 2010, to December 2011, the facility remanufactured 61,000 turbos. Presently the throughput is about 200 turbos per day. Each one takes about 21 minutes to complete from start to finish.
During the tour, highly skilled factory workers demonstrated the advanced processes they use to restore components to their original specifications. Turbo production includes creating new intake compressor wheels out of forged aluminum. Workers also repair damaged blades of the turbo exhaust intake using a precision welding technique. The Tooele facility is the only one in the world that has this advanced process which takes about 50 minutes to complete.
Before each turbo leaves the door, it is run through a flow stand to check performance under high and low pressure. The facility is only one of 5 in the world that has this flow technology.
The remanufactured products from Detroit Reman generally run between 70 and 80 percent of the cost of new parts. All of the parts from its six facilities are sold exclusively through Daimler Trucks of North America dealerships as Detroit Genuine Parts brand.
For more information, visit www.detroitreman.com