Jet Express
Dayton, Ohio
Improved CSA 2010 scores and raised company awareness by turning administrative and maintenance staff into trainers.
All together now
For Jet Express, CSA 2010 is more than the safety department and drivers
Jeff Davis realized long ago that the most effective way to manage safety isn’t always through the safety department. Davis, who is vice president of safety and human resources for Dayton, Ohio-based regional truckload carrier Jet Express, understands that drivers often respond better to managers and peers whose direct responsibilities aren’t in safety and compliance.
Involving personnel outside the safety department in safety coaching and observation sends the message that safety is, in a very real sense, everyone’s job, Davis says. And sometimes as powerful as helping drivers get this message is the impact on the whole company culture. Decentralizing safety helps encourage creativity in safety management, cultivating insights and perspectives different from those of Davis and his team.
Over the past couple of years, as the Federal Motor Carrier Safety Administration began to unveil detailed elements of its upcoming Comprehensive Safety Analysis 2010 initiative, Davis has been studying the new regime closely. Although Ohio is not one of the operational model test states and Davis hasn’t been involved operationally in CSA 2010, he has been a frequent presenter on the subject at industry association meetings. That’s a natural outgrowth of his encyclopedic knowledge of SafeStat, the current methodology FMCSA uses to target motor carriers for compliance reviews.
Davis familiarized himself thoroughly with the Safety Measurement System, which replaces SafeStat in December. Under CSA 2010, FMCSA is targeting more specific behaviors for earlier intervention and therefore is considering more information. So the SMS takes into account far more violations and weighs them according to FMCSA’s assessment of their severity. Even before FMCSA released to motor carriers their inspection and crash data through the lens of the seven Behavior Analysis and Safety Improvement Categories, or BASICs, earlier this year, Davis was crunching the raw data and looking at the BASICs himself.
Training the trainers
As everyone has realized in recent months, CSA 2010 requires training and awareness. Jet Express already had something of a head start because Davis has for years preached the fundamentals of safety enforcement under SafeStat. His basic point has been that roadside enforcement is a vicious circle. Safety events – such as driving 10 miles or more over the posted speed limit or having an obvious vehicle defect – lead to roadside inspections and more violations. As violations mount, inspection selection scores rise, which in turn leads to more routine inspections. So reducing safety events results in fewer violations, a lower inspection selection score and fewer routine inspections.
“CSA has a global impact across trucking companies.” – Jeff Davis, vice president of safety and human resources
This philosophy is all the more powerful in the CSA 2010 environment as the number of potential violations rises dramatically, Davis says. Indeed, non-out-of-service violations make up about 80 percent of all of Jet Express’ CSA 2010 points, he notes.
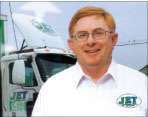
Ultimately, driver performance and behavior dictate a carrier’s CSA 2010 fate. But the people who manage and support those drivers are key because their behavior can either reinforce what drivers should be doing or run counter to it. “CSA has a global impact across trucking companies,” Davis notes. So when the time came this summer for Jet Express to begin spreading the word on CSA 2010 in earnest, he looked at the role administrative staff, mechanics and others could play not only in day-to-day management under CSA but also in training drivers.
After spending a few months analyzing Jet Express’ CSA numbers, Davis brought in about 40 nondriving employees for a “train the trainer” session during which he explained the circle of enforcement, the workings of CSA 2010, the top violations for the company and in which states most violations occur. Davis also trained personnel on the process of training truck drivers.
Following the session, Davis selected about half of the training class – with a heavy emphasis in operations and maintenance – to act as driver trainers. He selected the 30 drivers who had the highest CSA scores and assigned them to trainers. From that moment on, the trainer was accountable. “A trainer was absolutely responsible for the performance of that driver.” Davis observed a few of the initial training sessions, which were held over the first couple of weeks after the “train the trainer” session, but he tried to stay in the background and allow the trainers to interact with drivers in the way that best fit their personalities.
Each trainer is required to do two more follow-up training sessions with the driver within six months. Jet Express ranks the drivers each month; for the drivers there are cash prizes at stake.
Success so far
Davis acknowledges that it’s early, but preliminary results of the program are very encouraging. With two monthly data pulls since the training took place, none of the 30 high-point drivers has received a single additional CSA point. With those kind of results, Jet Express is expanding the “train the trainer” program and selecting some of its best drivers –10 at the Dayton terminal and 20 at the terminal in Marion, Ind. – to act as trainers.
Improving driver performance was the principal goal, but Davis has seen broader benefits from drawing more people into the CSA 2010 mindset. “We received a ton of suggestions and comments on how to do inspections better, work with drivers better and so on. Mid-level managers began to think through how they can improve things.”
One example of this creative thinking came from the maintenance staff at the Marion terminal. One of the mechanics involved in the “train the trainer” program suggested that trailers be given safety inspections coming into the shop as well as upon leaving the shop, which had been the practice. This approach makes for a more efficient use of limited bays because mechanics catch problems that they can fix while other work is being done rather than catching them just as the trailer otherwise would be ready to go. The shop foreman also changed the communication process so that drivers communicated known problems upon arriving at the shop.
Another change that came from the maintenance department related to the inspection of air hoses. During the “train the trainer” sessions, some mechanics had noticed that chaffing brake lines were the No. 4 violation in terms of point accumulations. Often it’s just the paint chipping off the hose, but it carries a severity point rating.
Given the impact of chaffing hoses on Jet Express’ CSA 2010 scores, the maintenance staff on their own initiative developed some special procedures for minimizing violations, including training on making sure that hoses are hung properly.
“That’s been the exciting part of it,” Davis says. Once people understood the key issues, they challenged themselves to tackle them. n
Innovators profiles carriers and fleets that have found innovative ways to overcome trucking’s challenges.
If you know a carrier that has displayed innovation, contact Jeff Crissey at [email protected] or 800-633-5953.