Sweat the small stuff
Today’s belts, hoses tougher, but still need care
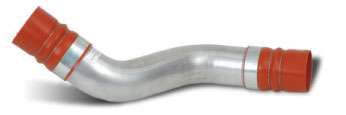
How often should technicians inspect belts and hoses? At every routine maintenance interval, according to some experts. Other less-conservative authorities say an appropriate maintenance interval depends on a truck’s vocation and ultimately should be geared to its duty cycle.
A good belting
The latest belts – those on trucks less than five years old – are made of a compound called EPDM (ethylene propylene diene monomer) rather than neoprene, which requires a different type of check for wear. While seeing a certain number of cracks in the ribs on the inner layer of the belt used to indicate wear, the different characteristics of the newer material mean a technician might not see more than an occasional crack for more than a million miles. “A visual inspection is no longer adequate,” says Matthew Duvall, heavy-duty product manager at Gates Corp.
The only effective procedure, Duvall says, is to use a special gauge placed over the ribs. Gates’ version – a small, simple plastic device his company provides – indicates wear similar to a tread depth gauge. If the gauge drops down below the ribs, “you’ll be able to see how much the ribs have worn,” he says.
Just as a tire will slip with excessive treadwear, the accessories of a serpentine belt’s ribs will slip with too much wear. Be aware of pulley abrasive wear, a critical problem in on- and off-road applications and construction where dust, debris and concrete are trapped between the belt and pulleys. Transit buses also see more pulley wear than highway trucks because the engines sit close to the street. But highway truck pulleys also deserve a check: Make sure they are configured properly to match the profiles of new belts, that the surfaces are smooth and undamaged, and to replace them if they become distorted through wear or are torn up.
Pulley misalignment is another problem; slippage, indicated by chirping, is a typical symptom. Misaligned pulleys often result when parts that are not matched properly to the application are used to replace OEM items that have failed, or adjustable items are not lined up properly. Brackets and other parts also can fatigue, causing axial misalignment that makes the belt flex side to side.
To check alignment, use sophisticated tools with a laser that provides a precise indication – within 1 or 2 degrees. As with tires, misalignment will be indicated by what Duvall describes as “uneven rib wear,” meaning wear that’s greater on one side of the belt than on the other.
Inspect belt tensioners first by observing them with the engine running. There should be little motion in the tensioner arm because the design includes a dampening function that works like a suspension’s shock absorber. If there is excessive oscillation in the arm, it indicates vibration is building up rather than the energy being removed, and that the tensioner should be replaced.
Also observe the width of the separation between the inner arm or “can” that holds the internal parts and its mount on the engine block. If the width is uneven or wider than when new – indicating the internal bearing is worn – the unit should be replaced. Even if it passes these tests, remember to still remove the belt and then rotate the arm through its full range of movement; the resistance should be steady and smooth. If binding is found, it probably has been attacked by dirt and debris and needs to be replaced.
Practice the latest maintenance techniques and pay attention to the details.
The latest trucks have larger cooling systems and alternators – the latter to help with anti-idling devices – which Duvall says means more demanding requirements for belts. Dual-sided micro V-belts with ribs on the back and front sides help drive the accessories more efficiently; make sure to replace these with the proper part and to buy only quality parts since they are more complex to manufacture.
Know your hoses
As far as checking hoses during routine inspections, heat is the enemy – whether from the outside air or the inside compressed air, coolant or other hot fluid – and makes the hose stiff and hard. The hose’s physical condition should be flexible and pliable; also check for leaks or discoloration from coolant. “It should not be cracked from proximity to an external heat source,” says Bill Morrissey, heavy-duty truck sales manager for FlexFab. Make sure it is not out of position on the coolant stem connection, which can occur if the hose was not installed properly or if clamps are undertorqued or have failed.
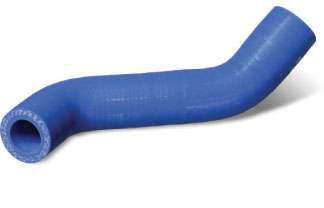
Is it necessary to check hose clamp torque? Constant tension clamps, if the torque is set properly at installation, will retain the pressure needed to seal as the hose expands and contracts with the engine’s normal heat cycle. Use high-quality constant-tension clamps and torque them to specification, Morrissey says.
What are the most important considerations to make when installing hoses? The Technology & Maintenance Council’s Recommended Practice No. 332 shows how to position clamps before torquing so they will hold. First, make sure the fittings are free of high or flat spots, damaged beads and dirt, and are not distorted in any way. After making sure the hose fits snugly around the fitting, install it – after the clamps are in position over the fittings – by using water or a weak soap and water solution as a lubricant until it is fully onto the fitting so that it touches the bead. Then install the clamp so it will be straight and one band-width or about 1/4-inch from the end of the hose. Clamps at the end of the hose or too far inside will be dislodged by internal pressure or hose expansion and contraction.
Constant torque-type clamps then must be torqued to specification with an inch-pound torque wrench. T-bolt clamps must be the proper size. When torqued properly, the gap between the loops at the ends of the band must be 0.19- to 0.75-inch wide; otherwise, the clamp will fail to conform properly to the hose.
When it’s time to replace hoses, both organic and silicone materials are available, Morrissey says. Silicone has both a higher and lower temperature operating range, which will result in longer life.
Don’t neglect A/C hoses, which tend to deteriorate from the inside out, shedding debris into the refrigerant or coolant. With the system in a static state, a technician should palpate the hose to gauge its firmness. “A technician’s hands are the simplest diagnostic tool available,” says Frank Burrow, manager of warranty and product support at Red Dot Corp., which manufactures HVAC units, systems and replacement parts for heavy-duty vehicles. “A spongy hose is a clear sign that it’s weak and should be replaced.”
A technician’s hands also can tell him if an A/C system is functioning properly. With the system running, the compressor discharge hose leading from the A/C compressor to the condenser behind the grille should feel hot – so hot, in fact, that a technician could burn himself if he touches it. “He should use the back of his hand to feel for heat radiating off the hose,” Burrow says. “If this hose isn’t hot, get a trained A/C technician on the case right away.”
If technicians follow these guidelines and quality parts are used for the proper application, trucks should end up getting new belts and hoses in the shop rather than during road calls. n