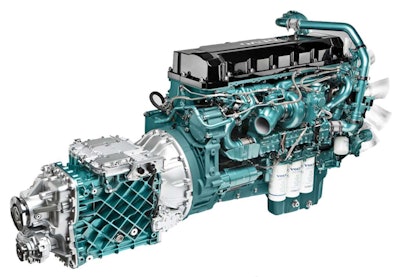
A downsped driveline lets the engine operate at its most efficient rpm, while also generating the minimal horsepower required to maintain a 65 mph cruise speed.
“There are a combination of factors for the engine fuel efficiency improvements,” says Meritor Senior Director of Rear Drivetrain Engineering Carlos Pinotti, “reduced engine friction due to lower piston speed, reduced heat transfer and flow losses due to lower gas velocities and improved thermodynamic efficiency.”
The lower the rpm, Eaton Application Engineering Mike Garrison says, the more you can reduce mpg-sucking drains on the drivetrain and boost engine efficiency.
“As you bring that engine rpm down 100 rpm or more, that reduces the friction, it reduces the parasitic losses and all that translates into fuel savings because the slower that engine is turning, you’re not running the water pumps, accessory drives and all those things nearly as fast,” he says, “not to mention fewer cycles per minute.”
Reduced heat and friction leads to less component wear, potentially extending the overall lifecycle of the engine.
“If you’re running that engine at 1150 rpm versus 1399,” says John Moore, Volvo Trucks North America powertrain product marketing manager, “that’s a lot less times the pistons have to travel up and down over its life, so the reliability is better.”
When Volvo debuted its XE13 package in 2011, rpm at cruise was reduced from about 1370 to about 1150. Newer iterations of downsped drivelines routinely cruise near 1050 rpm.
Every 100 rpm is worth about 1.5 percent in reduced fuel consumption, so being able to run highway speeds at 1150 rpm versus 1370 constitutes a fuel savings of more than 3 percent.
“Downspeeding is about reducing the amount of trips the piston takes up and down the engine, which reduces friction,” Moore says, “and this is actually where we’re saving the fuel.”
Similar to an aerodynamic package, all the pieces of a downsped driveline have to be spec’d to work together.
Engine downspeeding means a reduced input shaft speed with increased torque to deliver the same power to move the vehicle, which Pinotti says places increased load demand on the driveshaft at both highway speed and start-up.
Steve Slesinski, Dana’s director of global product planning for commercial vehicles notes as driveshaft speed slows down at highway cruise speed, the amount of torque going through both the driveshaft and axle system increases.
“Nobody cares about the driveshaft until it breaks or comes out of the vehicle,” adds Tom Bosler, Dana’s global driveshaft product management leader. “If you take a truck that was running at 1450 rpm down to about 1125, that rpm change of 325 rpm results in a 36 percent change in life [of the driveshaft and rear axles].”
At the maintenance level, Bosler says that means fleets who don’t spec a driveshaft compatible with a downsped driveline will see will see U-join failures approximately 36 percent sooner.
Scott Steurer, Application Engineer at Eaton, says group collaboration between component suppliers, like the Eaton Cummins venture, has helped to meld efficiencies through the driveline.
“The end result is the automation and the engine are talking more frequently, better, and making better shift decisions,” he says.
There are a lot of variables in play with downspeeding – engine spec, transmission-type and rear axle ratios to name a few – but much of the heavy lifting lies with the truck’s transmission.
The integrated driveline allows the system to calculate what Moore calls “perfect shift points” based on the truck’s load, road grade and needed torque.
Software options are flexible for application-specific needs and to promote performance or fuel economy, “and a variety of shifter packages go along with that,” he adds.
While the transmission’s software is optimized for downspeeding, the unit itself is mostly a stock AMT.
“The transmission knows how to hold the gears as long as possible to get the best payback on the fuel efficiency,” Moore says. “We never could downspeed with a manual transmission because a driver, every time he hit an overpass, would have to downshift to get over the overpass without losing too much speed. The driver would have to continually be shifting. If he got into some hilly terrain, that’s all he would be doing is shifting constantly. [A manual] doesn’t hold gears very well.”
After the transmission, Moore says selecting the proper rear axle ratio is vital.
When the Volvo XE package debuted, it featured a rear axle ratio of 2.64 – a gearing previously not found matched with an overdrive AMT.
“That was typically a direct drive ratio,” Moore says.