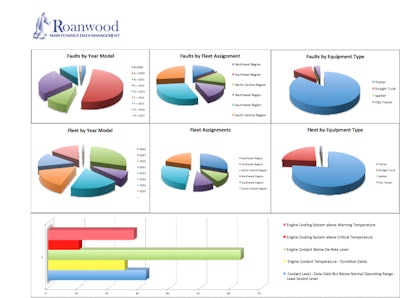
In the early 1990s, Ken Calhoun was working at a 500-truck fleet when the electronic era was ushered in by the on-highway Detroit Diesel Series 60 engine and its electronically controlled DDEC system.
Soon after, the fleet installed Qualcomm to track its vehicles and communicate with drivers. At the time, Calhoun observed that the diagnostics port for electronic engines was only three feet away from the Qualcomm devices.
“Why are they not talking to each other?” he wondered. Mobile computing providers would add that capability a few years later, but more recently, truck and engine manufacturers teamed up with them to create remote diagnostics services.
In 2010, Daimler Trucks of North America (DTNA) made Virtual Technician standard for all Freightliner trucks with EPA 2010 Detroit and newer engines. Whenever a fault code or “check engine” light appears, experts in Detroit’s Customer Support Center review and provide information to the vehicle owner and help schedule a repair, if necessary.
Likewise, Volvo and Mack made remote diagnostics standard on their vehicles. Navistar took a different approach with OnCommand Connect, an open diagnostics platform that receives telematics data from any source, make and model of truck.
All of these services are a valuable resource, but they presently do not help fleets “get in front of problems,” Calhoun says, since “you are reacting to information on one truck at a time.”
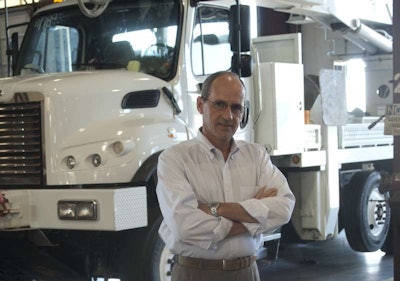
Further analysis of fault code data is needed to identify trends and to adjust preventive maintenance schedules to correct problems before they become critical situations, he says.
Earlier this year, a large utility fleet approached Calhoun with a problem. The fleet was a customer of Truck Centers of Arkansas, a DTNA dealership where Calhoun works as vice president of customer relations.
The fleet had installed telematics devices in its vehicles and began using Navistar’s OnCommand Connect portal. After a week, regional service managers at the company felt overwhelmed by data.
They were taking immediate actions when critical fault codes like a “stop engine” light appeared. All of the other non-critical fault code data seemed unmanageable, however.
“They asked me if I was interested in making sense of this,” he says.
In August, Calhoun was given login credentials to the fleet’s OnCommand Connect portal. He then created spreadsheet reports to turn fault-code data into information the fleet could use to improve the uptime of its vehicles and reduce costs.
The data management approach he uses is described below as a “How-To” guide to make sense of remote diagnostics data.
Step 1: Go after the low-hanging fruit.
From experience, Calhoun knows that more than one-third of all engine failures are triggered by a coolant failure. He therefore decided to focus on the five coolant-related fault codes that have the greatest impact on asset utilization. He ranked these five codes by severity from a low coolant warning on up to a critically high temperature warning.
Step 2: Remove the garbage.
Every morning, Calhoun exports data from OnCommand Connect into a spreadsheet template. He uses spreadsheet functions to filter out all non-critical fault codes that are unrelated to the cooling system. He also uses the “vlookup” function and pivot tables to marry and group fault code data by make, model, engine type and unit numbers of the vehicles for analysis.
Step 3: Take immediate actions.
Some fault codes need immediate, corrective actions. Drivers see a low coolant warning, for instance, on their dash display but other fault codes like “engine coolant below de-rate level” appear before the “check engine” light turns on.
The remedy for these two codes, in particular, is to add a gallon or two of coolant. When the codes repeat for a single vehicle it may be necessary to check the system for leaks. For these and other action items, Calhoun sends an e-mail to the maintenance manager.
Step 4: Spot monthly trends.
Calhoun maintains an ongoing dashboard-style report to monitor the frequency of fault codes that appear in categories that include the year, make and model of the vehicle and engine as well as persons responsible for maintenance of each vehicle. For each of these categories, fault codes are reported by frequency and compared to the total fleet population to identify the outliers.
Step 5: Make conclusions.
By comparing fault codes in each category to the total fleet population, Calhoun has found a number of interesting trends. For example, 2010 model-year units have 57 percent of all cooling system faults but are only 28 percent of the total vehicles in the fleet.
He also has found a greater percentage of fault codes by region. Another discovery is that Cummins ISB engines have greater longevity in some applications than larger Cummins ISC engines that generate more heat.
Step 6: Adjust PM schedules.
With the data analysis provided by Calhoun, the utility fleet is able to adjust its PM schedules. It is scheduling pressure checks for 2010 vehicles with cooling system fault codes during oil drain intervals. As the units are tracked month over month, the strategies have shown an impact by reducing fault codes and failures.
Calhoun has started a company, Roanwood Maintenance Data Management, that offers daily reporting and analysis services to fleets. The subscription service costs $75 per year, per truck. The cost is easily recovered by eliminating a tow bill or component repair, let alone a critical engine failure, he says.
For more information, Calhoun can be reached via e-mail at [email protected]